Latest Manufacturing Processes for Capacitor Dielectrics
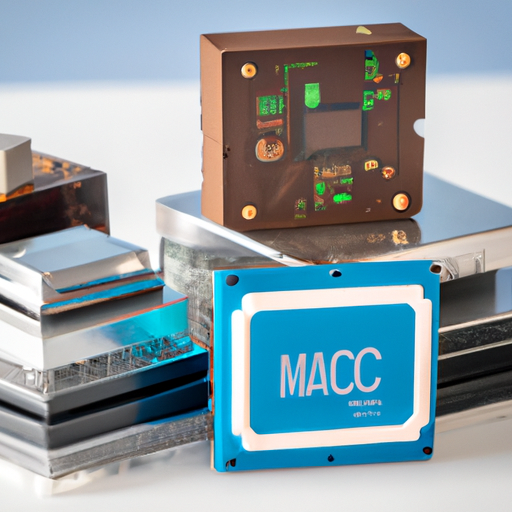
I. Introduction
Capacitors are essential components in electronic circuits, serving as energy storage devices that can release energy quickly when needed. At the heart of a capacitor's functionality lies its dielectric material, which separates the conductive plates and influences the capacitor's performance characteristics. The dielectric material's properties, such as permittivity, breakdown voltage, and thermal stability, are crucial for the efficiency and reliability of capacitors. As technology advances, the demand for high-performance capacitors has led to significant innovations in manufacturing processes for dielectric materials. This blog post explores the latest manufacturing processes for capacitor dielectrics, highlighting recent advancements and future trends.
II. Types of Capacitor Dielectrics
A. Ceramic Dielectrics
Ceramic dielectrics are widely used in capacitors due to their high dielectric strength and stability over a wide temperature range. They are commonly found in applications such as RF circuits, power electronics, and automotive systems. Recent innovations in ceramic dielectrics include the development of multilayer ceramic capacitors (MLCCs) that utilize advanced materials and processing techniques to achieve higher capacitance values in smaller packages. Researchers are also exploring new ceramic compositions that enhance dielectric properties while reducing costs.
B. Polymer Dielectrics
Polymer dielectrics, such as polyethylene terephthalate (PET) and polypropylene (PP), are known for their flexibility and lightweight characteristics. They are often used in applications requiring high capacitance and low weight, such as in portable electronics. Recent advancements in polymer dielectrics include the incorporation of nanomaterials to improve dielectric performance and thermal stability. Additionally, researchers are investigating the use of biodegradable polymers to create more sustainable capacitor options.
C. Electrolytic Dielectrics
Electrolytic capacitors utilize a liquid or gel electrolyte as the dielectric material, allowing for high capacitance values in a compact form factor. These capacitors are commonly used in power supply circuits and energy storage applications. Recent innovations in electrolytic dielectrics focus on improving the stability and lifespan of the electrolyte, as well as enhancing the overall performance of the capacitor. New formulations and manufacturing techniques are being developed to address issues such as leakage current and temperature sensitivity.
D. Other Emerging Dielectric Materials
1. Nanodielectrics
Nanodielectrics are materials that incorporate nanoparticles to enhance dielectric properties. These materials can significantly improve breakdown strength and thermal stability, making them ideal for high-performance capacitors. Recent research has focused on optimizing the dispersion of nanoparticles within the dielectric matrix to achieve the best performance.
2. Organic-Inorganic Hybrids
Organic-inorganic hybrid dielectrics combine the advantages of both organic and inorganic materials, resulting in improved dielectric properties and mechanical strength. These materials are gaining attention for their potential use in flexible electronics and high-density capacitors. Ongoing research aims to refine the synthesis processes and enhance the performance of these hybrid materials.
III. Traditional Manufacturing Processes
A. Overview of Conventional Techniques
Traditional manufacturing techniques for capacitor dielectrics include screen printing, tape casting, and sintering.
1. **Screen Printing**: This method involves applying a dielectric paste onto a substrate using a mesh screen. It is commonly used for producing multilayer capacitors but can be limited by the resolution and thickness of the printed layers.
2. **Tape Casting**: In this process, a slurry of dielectric material is spread onto a flat surface to create thin films. The films are then cut into desired shapes and sintered to achieve the final dielectric properties. While tape casting allows for uniform thickness, it can be time-consuming and may result in material waste.
3. **Sintering**: Sintering is a thermal process that fuses particles together to form a solid dielectric material. This method is essential for achieving the desired density and dielectric properties but can be limited by the need for high temperatures and long processing times.
B. Limitations of Traditional Methods
While traditional manufacturing processes have been effective, they also have limitations, including long production times, high energy consumption, and challenges in achieving uniformity and scalability. As the demand for advanced capacitors grows, there is a pressing need for more efficient and innovative manufacturing techniques.
IV. Advanced Manufacturing Techniques
A. Additive Manufacturing
1. 3D Printing of Dielectrics
Additive manufacturing, particularly 3D printing, is revolutionizing the production of capacitor dielectrics. This technique allows for the precise layering of materials, enabling the creation of complex geometries and customized designs. 3D printing can significantly reduce material waste and production time, making it an attractive option for manufacturers.
2. Benefits and Challenges
The benefits of 3D printing include design flexibility and the ability to produce small batches of customized capacitors. However, challenges remain, such as ensuring the dielectric properties of printed materials meet industry standards and optimizing the printing process for scalability.
B. Sol-Gel Processing
1. Process Overview
Sol-gel processing involves the transition of a solution (sol) into a solid (gel) phase, allowing for the fabrication of thin films and coatings with controlled microstructures. This method is particularly useful for producing high-purity dielectric materials with uniform properties.
2. Advantages for Dielectric Fabrication
Sol-gel processing offers several advantages, including low processing temperatures, the ability to incorporate various additives, and the potential for large-scale production. This technique is gaining traction for producing advanced ceramic and hybrid dielectrics.
C. Atomic Layer Deposition (ALD)
1. Mechanism and Applications
Atomic Layer Deposition (ALD) is a thin-film deposition technique that allows for the precise control of film thickness at the atomic level. This method is particularly beneficial for creating high-quality dielectric layers with excellent uniformity and conformality.
2. Impact on Dielectric Quality
ALD has been shown to enhance the dielectric properties of materials, making it a valuable tool for developing next-generation capacitors. Its ability to produce thin, uniform films can lead to improved performance and reliability in capacitors.
D. Chemical Vapor Deposition (CVD)
1. Process Overview
Chemical Vapor Deposition (CVD) is a process that involves the chemical reaction of gaseous precursors to form solid materials on a substrate. This technique is widely used for producing high-performance dielectric films.
2. Benefits for High-Performance Dielectrics
CVD offers several advantages, including the ability to create dense, uniform films with excellent adhesion to substrates. This method is particularly useful for producing dielectrics with high breakdown voltages and thermal stability.
E. Hybrid Manufacturing Techniques
1. Combining Methods for Enhanced Performance
Hybrid manufacturing techniques that combine traditional and advanced methods are emerging as a way to enhance the performance of capacitor dielectrics. For example, integrating 3D printing with sol-gel processing can lead to the production of complex structures with superior dielectric properties.
2. Case Studies
Several case studies have demonstrated the effectiveness of hybrid techniques in producing high-performance capacitors. These approaches often result in improved efficiency, reduced costs, and enhanced material properties.
V. Characterization and Quality Control
A. Importance of Characterization in Manufacturing
Characterization is critical in the manufacturing of capacitor dielectrics, as it ensures that the materials meet the required specifications and performance standards. Accurate characterization helps identify potential issues early in the production process.
B. Techniques for Evaluating Dielectric Properties
1. **Dielectric Constant Measurement**: This technique assesses the material's ability to store electrical energy, which is crucial for capacitor performance.
2. **Breakdown Voltage Testing**: This test determines the maximum voltage a dielectric material can withstand before failing, providing insights into its reliability.
3. **Thermal Stability Assessment**: Evaluating a dielectric's thermal stability is essential for ensuring its performance under varying temperature conditions.
C. Quality Control Measures in Manufacturing
Implementing robust quality control measures is vital for maintaining the consistency and reliability of capacitor dielectrics. This includes regular testing, process monitoring, and adherence to industry standards.
VI. Future Trends in Capacitor Dielectric Manufacturing
A. Integration of Smart Materials
The integration of smart materials into capacitor dielectrics is an emerging trend that promises to enhance performance and functionality. These materials can respond to external stimuli, enabling capacitors to adapt to changing conditions.
B. Sustainability and Eco-Friendly Processes
As environmental concerns grow, there is a push for more sustainable manufacturing processes in the capacitor industry. This includes the development of eco-friendly materials and processes that minimize waste and energy consumption.
C. Miniaturization and High-Efficiency Designs
The trend toward miniaturization in electronics is driving the demand for smaller, more efficient capacitors. Manufacturers are focusing on developing dielectrics that can achieve high capacitance values in compact designs.
D. Role of Artificial Intelligence and Machine Learning
Artificial intelligence (AI) and machine learning are increasingly being used to optimize manufacturing processes and improve material design. These technologies can analyze vast amounts of data to identify patterns and predict performance, leading to more efficient and effective manufacturing.
VII. Conclusion
The manufacturing processes for capacitor dielectrics are evolving rapidly, driven by advancements in materials science and technology. From traditional methods to innovative techniques like 3D printing and sol-gel processing, the industry is witnessing significant improvements in performance, efficiency, and sustainability. As we look to the future, the integration of smart materials, eco-friendly processes, and AI-driven optimization will play a crucial role in shaping the next generation of capacitor dielectrics. The ongoing innovations in this field will not only enhance the performance of capacitors but also contribute to the development of more sustainable and efficient electronic devices.
VIII. References
A comprehensive list of academic journals, industry reports, and relevant books and articles would be included here to support the information presented in the blog post.
Latest Manufacturing Processes for Capacitor Dielectrics
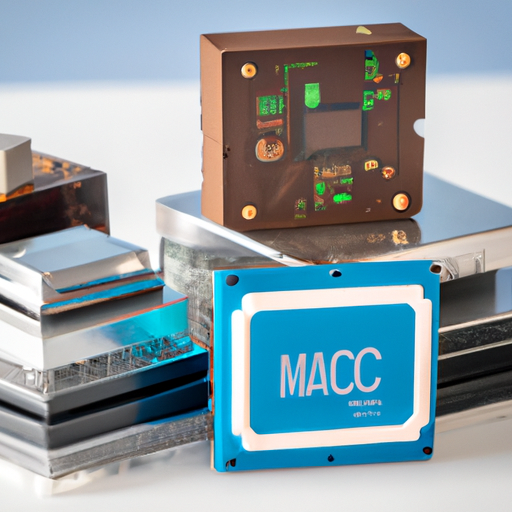
I. Introduction
Capacitors are essential components in electronic circuits, serving as energy storage devices that can release energy quickly when needed. At the heart of a capacitor's functionality lies its dielectric material, which separates the conductive plates and influences the capacitor's performance characteristics. The dielectric material's properties, such as permittivity, breakdown voltage, and thermal stability, are crucial for the efficiency and reliability of capacitors. As technology advances, the demand for high-performance capacitors has led to significant innovations in manufacturing processes for dielectric materials. This blog post explores the latest manufacturing processes for capacitor dielectrics, highlighting recent advancements and future trends.
II. Types of Capacitor Dielectrics
A. Ceramic Dielectrics
Ceramic dielectrics are widely used in capacitors due to their high dielectric strength and stability over a wide temperature range. They are commonly found in applications such as RF circuits, power electronics, and automotive systems. Recent innovations in ceramic dielectrics include the development of multilayer ceramic capacitors (MLCCs) that utilize advanced materials and processing techniques to achieve higher capacitance values in smaller packages. Researchers are also exploring new ceramic compositions that enhance dielectric properties while reducing costs.
B. Polymer Dielectrics
Polymer dielectrics, such as polyethylene terephthalate (PET) and polypropylene (PP), are known for their flexibility and lightweight characteristics. They are often used in applications requiring high capacitance and low weight, such as in portable electronics. Recent advancements in polymer dielectrics include the incorporation of nanomaterials to improve dielectric performance and thermal stability. Additionally, researchers are investigating the use of biodegradable polymers to create more sustainable capacitor options.
C. Electrolytic Dielectrics
Electrolytic capacitors utilize a liquid or gel electrolyte as the dielectric material, allowing for high capacitance values in a compact form factor. These capacitors are commonly used in power supply circuits and energy storage applications. Recent innovations in electrolytic dielectrics focus on improving the stability and lifespan of the electrolyte, as well as enhancing the overall performance of the capacitor. New formulations and manufacturing techniques are being developed to address issues such as leakage current and temperature sensitivity.
D. Other Emerging Dielectric Materials
1. Nanodielectrics
Nanodielectrics are materials that incorporate nanoparticles to enhance dielectric properties. These materials can significantly improve breakdown strength and thermal stability, making them ideal for high-performance capacitors. Recent research has focused on optimizing the dispersion of nanoparticles within the dielectric matrix to achieve the best performance.
2. Organic-Inorganic Hybrids
Organic-inorganic hybrid dielectrics combine the advantages of both organic and inorganic materials, resulting in improved dielectric properties and mechanical strength. These materials are gaining attention for their potential use in flexible electronics and high-density capacitors. Ongoing research aims to refine the synthesis processes and enhance the performance of these hybrid materials.
III. Traditional Manufacturing Processes
A. Overview of Conventional Techniques
Traditional manufacturing techniques for capacitor dielectrics include screen printing, tape casting, and sintering.
1. **Screen Printing**: This method involves applying a dielectric paste onto a substrate using a mesh screen. It is commonly used for producing multilayer capacitors but can be limited by the resolution and thickness of the printed layers.
2. **Tape Casting**: In this process, a slurry of dielectric material is spread onto a flat surface to create thin films. The films are then cut into desired shapes and sintered to achieve the final dielectric properties. While tape casting allows for uniform thickness, it can be time-consuming and may result in material waste.
3. **Sintering**: Sintering is a thermal process that fuses particles together to form a solid dielectric material. This method is essential for achieving the desired density and dielectric properties but can be limited by the need for high temperatures and long processing times.
B. Limitations of Traditional Methods
While traditional manufacturing processes have been effective, they also have limitations, including long production times, high energy consumption, and challenges in achieving uniformity and scalability. As the demand for advanced capacitors grows, there is a pressing need for more efficient and innovative manufacturing techniques.
IV. Advanced Manufacturing Techniques
A. Additive Manufacturing
1. 3D Printing of Dielectrics
Additive manufacturing, particularly 3D printing, is revolutionizing the production of capacitor dielectrics. This technique allows for the precise layering of materials, enabling the creation of complex geometries and customized designs. 3D printing can significantly reduce material waste and production time, making it an attractive option for manufacturers.
2. Benefits and Challenges
The benefits of 3D printing include design flexibility and the ability to produce small batches of customized capacitors. However, challenges remain, such as ensuring the dielectric properties of printed materials meet industry standards and optimizing the printing process for scalability.
B. Sol-Gel Processing
1. Process Overview
Sol-gel processing involves the transition of a solution (sol) into a solid (gel) phase, allowing for the fabrication of thin films and coatings with controlled microstructures. This method is particularly useful for producing high-purity dielectric materials with uniform properties.
2. Advantages for Dielectric Fabrication
Sol-gel processing offers several advantages, including low processing temperatures, the ability to incorporate various additives, and the potential for large-scale production. This technique is gaining traction for producing advanced ceramic and hybrid dielectrics.
C. Atomic Layer Deposition (ALD)
1. Mechanism and Applications
Atomic Layer Deposition (ALD) is a thin-film deposition technique that allows for the precise control of film thickness at the atomic level. This method is particularly beneficial for creating high-quality dielectric layers with excellent uniformity and conformality.
2. Impact on Dielectric Quality
ALD has been shown to enhance the dielectric properties of materials, making it a valuable tool for developing next-generation capacitors. Its ability to produce thin, uniform films can lead to improved performance and reliability in capacitors.
D. Chemical Vapor Deposition (CVD)
1. Process Overview
Chemical Vapor Deposition (CVD) is a process that involves the chemical reaction of gaseous precursors to form solid materials on a substrate. This technique is widely used for producing high-performance dielectric films.
2. Benefits for High-Performance Dielectrics
CVD offers several advantages, including the ability to create dense, uniform films with excellent adhesion to substrates. This method is particularly useful for producing dielectrics with high breakdown voltages and thermal stability.
E. Hybrid Manufacturing Techniques
1. Combining Methods for Enhanced Performance
Hybrid manufacturing techniques that combine traditional and advanced methods are emerging as a way to enhance the performance of capacitor dielectrics. For example, integrating 3D printing with sol-gel processing can lead to the production of complex structures with superior dielectric properties.
2. Case Studies
Several case studies have demonstrated the effectiveness of hybrid techniques in producing high-performance capacitors. These approaches often result in improved efficiency, reduced costs, and enhanced material properties.
V. Characterization and Quality Control
A. Importance of Characterization in Manufacturing
Characterization is critical in the manufacturing of capacitor dielectrics, as it ensures that the materials meet the required specifications and performance standards. Accurate characterization helps identify potential issues early in the production process.
B. Techniques for Evaluating Dielectric Properties
1. **Dielectric Constant Measurement**: This technique assesses the material's ability to store electrical energy, which is crucial for capacitor performance.
2. **Breakdown Voltage Testing**: This test determines the maximum voltage a dielectric material can withstand before failing, providing insights into its reliability.
3. **Thermal Stability Assessment**: Evaluating a dielectric's thermal stability is essential for ensuring its performance under varying temperature conditions.
C. Quality Control Measures in Manufacturing
Implementing robust quality control measures is vital for maintaining the consistency and reliability of capacitor dielectrics. This includes regular testing, process monitoring, and adherence to industry standards.
VI. Future Trends in Capacitor Dielectric Manufacturing
A. Integration of Smart Materials
The integration of smart materials into capacitor dielectrics is an emerging trend that promises to enhance performance and functionality. These materials can respond to external stimuli, enabling capacitors to adapt to changing conditions.
B. Sustainability and Eco-Friendly Processes
As environmental concerns grow, there is a push for more sustainable manufacturing processes in the capacitor industry. This includes the development of eco-friendly materials and processes that minimize waste and energy consumption.
C. Miniaturization and High-Efficiency Designs
The trend toward miniaturization in electronics is driving the demand for smaller, more efficient capacitors. Manufacturers are focusing on developing dielectrics that can achieve high capacitance values in compact designs.
D. Role of Artificial Intelligence and Machine Learning
Artificial intelligence (AI) and machine learning are increasingly being used to optimize manufacturing processes and improve material design. These technologies can analyze vast amounts of data to identify patterns and predict performance, leading to more efficient and effective manufacturing.
VII. Conclusion
The manufacturing processes for capacitor dielectrics are evolving rapidly, driven by advancements in materials science and technology. From traditional methods to innovative techniques like 3D printing and sol-gel processing, the industry is witnessing significant improvements in performance, efficiency, and sustainability. As we look to the future, the integration of smart materials, eco-friendly processes, and AI-driven optimization will play a crucial role in shaping the next generation of capacitor dielectrics. The ongoing innovations in this field will not only enhance the performance of capacitors but also contribute to the development of more sustainable and efficient electronic devices.
VIII. References
A comprehensive list of academic journals, industry reports, and relevant books and articles would be included here to support the information presented in the blog post.