The Production Process of Mainstream Battery Capacitors
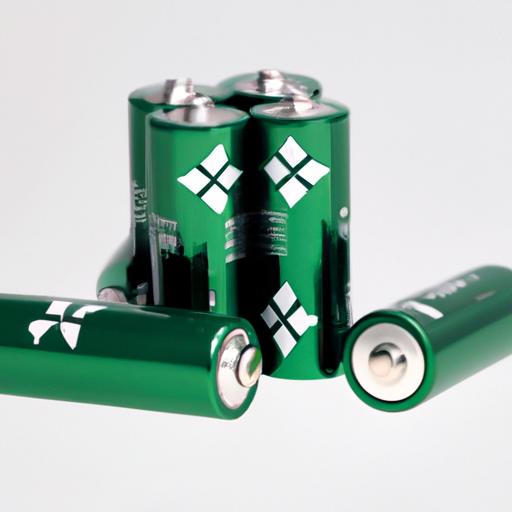
I. Introduction
In the realm of modern technology, battery capacitors play a pivotal role in energy storage and management. These components, which store and release electrical energy, are essential in various applications, from consumer electronics to electric vehicles and renewable energy systems. Understanding the production process of mainstream battery capacitors is crucial for appreciating their significance and the innovations driving their development.
II. Types of Battery Capacitors
Battery capacitors come in several types, each with unique characteristics and applications:
A. Electrolytic Capacitors
Electrolytic capacitors are widely used due to their high capacitance values and compact size. They utilize an electrolyte to achieve a larger surface area for charge storage, making them ideal for power supply applications.
B. Ceramic Capacitors
Ceramic capacitors are known for their stability and reliability. They are often used in high-frequency applications and are favored for their small size and low cost.
C. Film Capacitors
Film capacitors are made from thin plastic films and are known for their excellent performance in high-voltage applications. They are often used in audio equipment and power electronics.
D. Supercapacitors
Supercapacitors, or ultracapacitors, bridge the gap between traditional capacitors and batteries. They offer high energy density and rapid charge/discharge capabilities, making them suitable for applications requiring quick bursts of energy.
E. Comparison of Different Types
While all these capacitors serve the purpose of energy storage, their applications vary based on their characteristics. Electrolytic capacitors are preferred for bulk energy storage, while supercapacitors excel in applications requiring rapid energy delivery.
III. Raw Materials
The production of battery capacitors begins with the careful selection of raw materials.
A. Overview of Materials Used in Battery Capacitors
1. **Dielectric Materials**: These materials, which can be ceramic, plastic, or electrolytic, are crucial for separating the capacitor's plates and storing electrical energy.
2. **Conductive Materials**: Metals such as aluminum and tantalum are commonly used for electrodes due to their excellent conductivity.
3. **Electrolytes**: In electrolytic capacitors, the electrolyte facilitates ion movement, which is essential for charge storage.
B. Sourcing and Quality Control of Raw Materials
Sourcing high-quality raw materials is vital for ensuring the performance and reliability of battery capacitors. Manufacturers often implement stringent quality control measures to verify the purity and consistency of materials before production.
IV. Design and Engineering
The design and engineering phase is critical in determining the performance characteristics of battery capacitors.
A. Initial Design Considerations
1. **Capacitance Requirements**: Engineers must define the capacitance needed for the intended application, which influences the size and type of capacitor.
2. **Voltage Ratings**: The voltage rating is crucial for ensuring the capacitor can operate safely within its intended environment.
3. **Size and Form Factor**: The physical dimensions of the capacitor must align with the design constraints of the final product.
B. Simulation and Modeling
Advanced simulation tools allow engineers to model the behavior of capacitors under various conditions, optimizing their design before physical prototypes are created.
C. Prototyping and Testing
Prototyping is essential for validating design choices. Engineers create initial samples to test performance, reliability, and compliance with specifications.
V. Manufacturing Process
The manufacturing process of battery capacitors involves several key steps:
A. Step 1: Preparation of Materials
1. **Cleaning and Treating Raw Materials**: Ensuring that all materials are free from contaminants is crucial for performance.
2. **Mixing and Compounding**: Raw materials are mixed to create the dielectric and conductive components, ensuring uniformity.
B. Step 2: Dielectric Layer Formation
1. **Techniques for Dielectric Layer Application**: Various methods, such as coating or layering, are used to apply the dielectric material.
2. **Curing and Drying Processes**: The dielectric layer must be cured and dried to achieve the desired properties.
C. Step 3: Electrode Fabrication
1. **Methods for Creating Electrodes**: Electrodes are typically created through processes like sputtering or chemical vapor deposition.
2. **Application of Conductive Materials**: Conductive materials are applied to the electrodes to enhance their performance.
D. Step 4: Assembly
1. **Layer Stacking and Alignment**: The dielectric and electrode layers are carefully stacked and aligned to ensure optimal performance.
2. **Encapsulation and Sealing**: The assembled capacitor is encapsulated to protect it from environmental factors.
E. Step 5: Electrolyte Filling
1. **Techniques for Electrolyte Application**: The electrolyte is introduced into the capacitor using methods that ensure uniform distribution.
2. **Ensuring Uniform Distribution**: Proper filling techniques are critical for the capacitor's performance and longevity.
F. Step 6: Final Testing and Quality Control
1. **Electrical Testing**: Capacitors undergo rigorous electrical testing to verify their performance against specifications.
2. **Physical Inspections**: Visual inspections ensure that there are no defects in the physical structure.
3. **Reliability Testing**: Long-term reliability tests are conducted to ensure the capacitor will perform over its expected lifespan.
VI. Environmental Considerations
As the demand for battery capacitors grows, so does the need for sustainable practices in their production.
A. Waste Management in Capacitor Production
Manufacturers are increasingly focusing on waste reduction strategies, implementing recycling programs, and minimizing the environmental impact of their operations.
B. Recycling of Battery Capacitors
Recycling programs are essential for recovering valuable materials from end-of-life capacitors, reducing the need for new raw materials and minimizing waste.
C. Compliance with Environmental Regulations
Manufacturers must adhere to environmental regulations to ensure their production processes are sustainable and responsible.
VII. Future Trends in Battery Capacitor Production
The future of battery capacitor production is poised for significant advancements.
A. Innovations in Materials and Technology
Research into new materials, such as graphene and advanced polymers, promises to enhance the performance and efficiency of battery capacitors.
B. The Impact of Electric Vehicles and Renewable Energy
The rise of electric vehicles and renewable energy sources is driving demand for high-performance capacitors, leading to innovations in design and manufacturing processes.
C. Potential for Miniaturization and Increased Efficiency
As technology advances, the trend toward miniaturization and increased efficiency in battery capacitors will continue, enabling more compact and powerful energy storage solutions.
VIII. Conclusion
The production process of mainstream battery capacitors is a complex and multifaceted endeavor that involves careful consideration of materials, design, and manufacturing techniques. As technology continues to evolve, the significance of battery capacitors in energy storage and management will only grow. Continued research and development in this field are essential for meeting the demands of future technologies, particularly in the realms of electric vehicles and renewable energy. By understanding the production process, we can appreciate the critical role that battery capacitors play in shaping a sustainable and technologically advanced future.
The Production Process of Mainstream Battery Capacitors
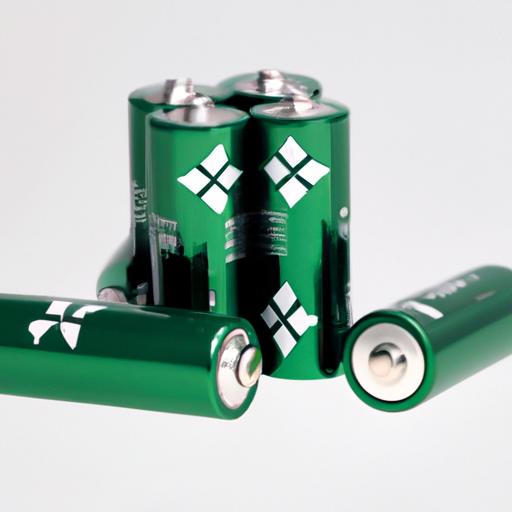
I. Introduction
In the realm of modern technology, battery capacitors play a pivotal role in energy storage and management. These components, which store and release electrical energy, are essential in various applications, from consumer electronics to electric vehicles and renewable energy systems. Understanding the production process of mainstream battery capacitors is crucial for appreciating their significance and the innovations driving their development.
II. Types of Battery Capacitors
Battery capacitors come in several types, each with unique characteristics and applications:
A. Electrolytic Capacitors
Electrolytic capacitors are widely used due to their high capacitance values and compact size. They utilize an electrolyte to achieve a larger surface area for charge storage, making them ideal for power supply applications.
B. Ceramic Capacitors
Ceramic capacitors are known for their stability and reliability. They are often used in high-frequency applications and are favored for their small size and low cost.
C. Film Capacitors
Film capacitors are made from thin plastic films and are known for their excellent performance in high-voltage applications. They are often used in audio equipment and power electronics.
D. Supercapacitors
Supercapacitors, or ultracapacitors, bridge the gap between traditional capacitors and batteries. They offer high energy density and rapid charge/discharge capabilities, making them suitable for applications requiring quick bursts of energy.
E. Comparison of Different Types
While all these capacitors serve the purpose of energy storage, their applications vary based on their characteristics. Electrolytic capacitors are preferred for bulk energy storage, while supercapacitors excel in applications requiring rapid energy delivery.
III. Raw Materials
The production of battery capacitors begins with the careful selection of raw materials.
A. Overview of Materials Used in Battery Capacitors
1. **Dielectric Materials**: These materials, which can be ceramic, plastic, or electrolytic, are crucial for separating the capacitor's plates and storing electrical energy.
2. **Conductive Materials**: Metals such as aluminum and tantalum are commonly used for electrodes due to their excellent conductivity.
3. **Electrolytes**: In electrolytic capacitors, the electrolyte facilitates ion movement, which is essential for charge storage.
B. Sourcing and Quality Control of Raw Materials
Sourcing high-quality raw materials is vital for ensuring the performance and reliability of battery capacitors. Manufacturers often implement stringent quality control measures to verify the purity and consistency of materials before production.
IV. Design and Engineering
The design and engineering phase is critical in determining the performance characteristics of battery capacitors.
A. Initial Design Considerations
1. **Capacitance Requirements**: Engineers must define the capacitance needed for the intended application, which influences the size and type of capacitor.
2. **Voltage Ratings**: The voltage rating is crucial for ensuring the capacitor can operate safely within its intended environment.
3. **Size and Form Factor**: The physical dimensions of the capacitor must align with the design constraints of the final product.
B. Simulation and Modeling
Advanced simulation tools allow engineers to model the behavior of capacitors under various conditions, optimizing their design before physical prototypes are created.
C. Prototyping and Testing
Prototyping is essential for validating design choices. Engineers create initial samples to test performance, reliability, and compliance with specifications.
V. Manufacturing Process
The manufacturing process of battery capacitors involves several key steps:
A. Step 1: Preparation of Materials
1. **Cleaning and Treating Raw Materials**: Ensuring that all materials are free from contaminants is crucial for performance.
2. **Mixing and Compounding**: Raw materials are mixed to create the dielectric and conductive components, ensuring uniformity.
B. Step 2: Dielectric Layer Formation
1. **Techniques for Dielectric Layer Application**: Various methods, such as coating or layering, are used to apply the dielectric material.
2. **Curing and Drying Processes**: The dielectric layer must be cured and dried to achieve the desired properties.
C. Step 3: Electrode Fabrication
1. **Methods for Creating Electrodes**: Electrodes are typically created through processes like sputtering or chemical vapor deposition.
2. **Application of Conductive Materials**: Conductive materials are applied to the electrodes to enhance their performance.
D. Step 4: Assembly
1. **Layer Stacking and Alignment**: The dielectric and electrode layers are carefully stacked and aligned to ensure optimal performance.
2. **Encapsulation and Sealing**: The assembled capacitor is encapsulated to protect it from environmental factors.
E. Step 5: Electrolyte Filling
1. **Techniques for Electrolyte Application**: The electrolyte is introduced into the capacitor using methods that ensure uniform distribution.
2. **Ensuring Uniform Distribution**: Proper filling techniques are critical for the capacitor's performance and longevity.
F. Step 6: Final Testing and Quality Control
1. **Electrical Testing**: Capacitors undergo rigorous electrical testing to verify their performance against specifications.
2. **Physical Inspections**: Visual inspections ensure that there are no defects in the physical structure.
3. **Reliability Testing**: Long-term reliability tests are conducted to ensure the capacitor will perform over its expected lifespan.
VI. Environmental Considerations
As the demand for battery capacitors grows, so does the need for sustainable practices in their production.
A. Waste Management in Capacitor Production
Manufacturers are increasingly focusing on waste reduction strategies, implementing recycling programs, and minimizing the environmental impact of their operations.
B. Recycling of Battery Capacitors
Recycling programs are essential for recovering valuable materials from end-of-life capacitors, reducing the need for new raw materials and minimizing waste.
C. Compliance with Environmental Regulations
Manufacturers must adhere to environmental regulations to ensure their production processes are sustainable and responsible.
VII. Future Trends in Battery Capacitor Production
The future of battery capacitor production is poised for significant advancements.
A. Innovations in Materials and Technology
Research into new materials, such as graphene and advanced polymers, promises to enhance the performance and efficiency of battery capacitors.
B. The Impact of Electric Vehicles and Renewable Energy
The rise of electric vehicles and renewable energy sources is driving demand for high-performance capacitors, leading to innovations in design and manufacturing processes.
C. Potential for Miniaturization and Increased Efficiency
As technology advances, the trend toward miniaturization and increased efficiency in battery capacitors will continue, enabling more compact and powerful energy storage solutions.
VIII. Conclusion
The production process of mainstream battery capacitors is a complex and multifaceted endeavor that involves careful consideration of materials, design, and manufacturing techniques. As technology continues to evolve, the significance of battery capacitors in energy storage and management will only grow. Continued research and development in this field are essential for meeting the demands of future technologies, particularly in the realms of electric vehicles and renewable energy. By understanding the production process, we can appreciate the critical role that battery capacitors play in shaping a sustainable and technologically advanced future.