What are the Product Standards for Aluminum Capacitors?
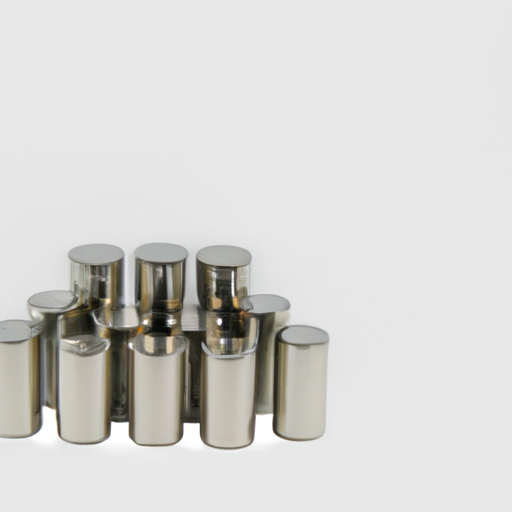
I. Introduction
Aluminum capacitors are essential components in a wide range of electronic devices, from consumer electronics to industrial machinery. These capacitors store and release electrical energy, playing a crucial role in circuit performance. As the demand for reliable and efficient electronic components grows, so does the importance of adhering to product standards. This article aims to explore the product standards for aluminum capacitors, highlighting their significance, key standards, testing processes, compliance, and future trends.
II. Understanding Aluminum Capacitors
A. Basic Principles of Aluminum Capacitors
Aluminum capacitors are constructed using aluminum foil as one of the electrodes, with an electrolyte that serves as the dielectric. The basic construction involves two aluminum plates separated by a thin layer of oxide, which acts as an insulator. When voltage is applied, an electric field is created, allowing the capacitor to store energy.
There are various types of aluminum capacitors, including electrolytic capacitors, which are polarized and typically used in applications requiring high capacitance values, and non-polarized capacitors, which can be used in AC circuits.
B. Applications of Aluminum Capacitors
Aluminum capacitors are widely used across different sectors:
1. **Consumer Electronics**: They are found in devices such as televisions, computers, and smartphones, where they help stabilize voltage and filter signals.
2. **Industrial Applications**: In industrial settings, aluminum capacitors are used in power supplies, motor drives, and automation systems, where reliability is critical.
3. **Automotive Uses**: In the automotive industry, these capacitors are employed in various electronic control units (ECUs), infotainment systems, and safety features, ensuring optimal performance under varying conditions.
III. Importance of Product Standards
A. Ensuring Safety and Reliability
Product standards are vital for ensuring the safety and reliability of aluminum capacitors. They provide guidelines for manufacturers to follow, minimizing the risk of failures that could lead to hazardous situations, such as overheating or explosions.
B. Facilitating International Trade
Adhering to recognized product standards facilitates international trade by ensuring that products meet specific quality and safety requirements. This harmonization allows manufacturers to market their products globally without facing regulatory barriers.
C. Promoting Technological Advancement and Innovation
Standards encourage innovation by setting benchmarks for performance and quality. Manufacturers are motivated to improve their products to meet or exceed these standards, leading to advancements in technology and materials.
IV. Key Product Standards for Aluminum Capacitors
A. International Standards
1. **IEC (International Electrotechnical Commission)**: The IEC sets several standards for aluminum capacitors, including:
- **IEC 60384 Series**: This series covers fixed capacitors for use in electronic equipment, detailing performance requirements and testing methods.
- **IEC 61071**: This standard specifies the requirements for capacitors used in power electronics.
2. **ISO (International Organization for Standardization)**:
- **ISO 9001**: This standard focuses on quality management systems, ensuring that manufacturers maintain consistent quality in their production processes.
B. National Standards
1. **ANSI (American National Standards Institute)**: ANSI develops standards that ensure the safety and performance of aluminum capacitors in the United States.
2. **JIS (Japanese Industrial Standards)**: JIS provides guidelines for the manufacturing and testing of aluminum capacitors in Japan.
3. **GB (Guobiao Standards in China)**: GB standards govern the quality and safety of electronic components, including aluminum capacitors, in China.
C. Industry-Specific Standards
1. **Automotive Standards (e.g., AEC-Q200)**: This standard outlines the qualification requirements for passive components used in automotive applications, ensuring reliability under harsh conditions.
2. **Military Standards (e.g., MIL-PRF-39018)**: These standards specify the performance and reliability requirements for capacitors used in military applications, where failure is not an option.
V. Testing and Certification Processes
A. Overview of Testing Methods
To ensure compliance with product standards, aluminum capacitors undergo rigorous testing, including:
1. **Electrical Testing**: This includes measuring capacitance, equivalent series resistance (ESR), and leakage current to ensure the capacitor performs as expected.
2. **Environmental Testing**: Capacitors are subjected to various environmental conditions, such as temperature extremes, humidity, and vibration, to assess their durability and reliability.
B. Certification Bodies and Their Roles
Several certification bodies play a crucial role in the testing and certification of aluminum capacitors:
1. **UL (Underwriters Laboratories)**: UL provides safety certification for electronic components, ensuring they meet specific safety standards.
2. **TUV (Technischer Überwachungsverein)**: TUV offers testing and certification services, focusing on product safety and quality.
3. **CSA (Canadian Standards Association)**: CSA certifies products for compliance with Canadian safety standards, ensuring they are safe for use in the Canadian market.
VI. Compliance and Quality Assurance
A. Importance of Compliance with Standards
Compliance with product standards is essential for manufacturers to ensure their products are safe, reliable, and of high quality. Non-compliance can lead to product recalls, legal issues, and damage to a company's reputation.
B. Quality Assurance Processes in Manufacturing
Manufacturers implement various quality assurance processes to maintain compliance with standards:
1. **Incoming Material Inspection**: Raw materials are inspected upon arrival to ensure they meet specified quality standards.
2. **In-Process Quality Control**: Throughout the manufacturing process, quality control measures are implemented to monitor production and identify any deviations from standards.
3. **Final Product Testing**: Before products are shipped, they undergo final testing to verify that they meet all performance and safety requirements.
VII. Challenges in Meeting Product Standards
A. Technological Advancements and Evolving Standards
As technology evolves, so do product standards. Manufacturers must continuously adapt to new requirements, which can be challenging and resource-intensive.
B. Global Supply Chain Issues
Global supply chain disruptions can impact the availability of materials and components, making it difficult for manufacturers to meet standards consistently.
C. Balancing Cost and Compliance
Manufacturers often face the challenge of balancing the costs associated with compliance and quality assurance with the need to remain competitive in the market.
VIII. Future Trends in Aluminum Capacitor Standards
A. Innovations in Materials and Technology
The future of aluminum capacitors will likely see innovations in materials and technology, leading to improved performance and efficiency. New dielectric materials and manufacturing techniques may enhance capacitance and reduce size.
B. Increasing Focus on Sustainability and Environmental Impact
As environmental concerns grow, there will be an increasing focus on sustainability in the production of aluminum capacitors. Manufacturers may adopt eco-friendly materials and processes to minimize their environmental footprint.
C. Anticipated Changes in Regulatory Frameworks
Regulatory frameworks are expected to evolve, with stricter standards for safety and environmental impact. Manufacturers will need to stay informed and adapt to these changes to remain compliant.
IX. Conclusion
In conclusion, product standards for aluminum capacitors play a vital role in ensuring safety, reliability, and quality in electronic components. These standards facilitate international trade, promote technological advancement, and help manufacturers maintain compliance. As the industry evolves, staying abreast of key standards, testing processes, and future trends will be essential for manufacturers to succeed in a competitive market.
X. References
1. IEC 60384 Series - Fixed capacitors for use in electronic equipment.
2. ISO 9001 - Quality Management Systems.
3. AEC-Q200 - Qualification of passive components for automotive applications.
4. MIL-PRF-39018 - Military specification for capacitors.
5. UL, TUV, and CSA certification guidelines.
This comprehensive overview of product standards for aluminum capacitors highlights their significance in the electronics industry and provides insights into the future of these essential components.
What are the Product Standards for Aluminum Capacitors?
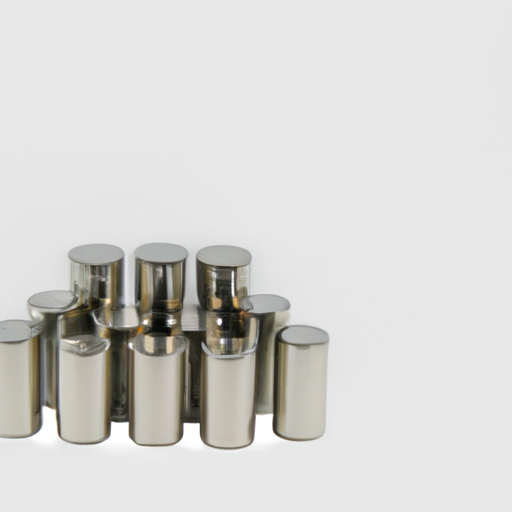
I. Introduction
Aluminum capacitors are essential components in a wide range of electronic devices, from consumer electronics to industrial machinery. These capacitors store and release electrical energy, playing a crucial role in circuit performance. As the demand for reliable and efficient electronic components grows, so does the importance of adhering to product standards. This article aims to explore the product standards for aluminum capacitors, highlighting their significance, key standards, testing processes, compliance, and future trends.
II. Understanding Aluminum Capacitors
A. Basic Principles of Aluminum Capacitors
Aluminum capacitors are constructed using aluminum foil as one of the electrodes, with an electrolyte that serves as the dielectric. The basic construction involves two aluminum plates separated by a thin layer of oxide, which acts as an insulator. When voltage is applied, an electric field is created, allowing the capacitor to store energy.
There are various types of aluminum capacitors, including electrolytic capacitors, which are polarized and typically used in applications requiring high capacitance values, and non-polarized capacitors, which can be used in AC circuits.
B. Applications of Aluminum Capacitors
Aluminum capacitors are widely used across different sectors:
1. **Consumer Electronics**: They are found in devices such as televisions, computers, and smartphones, where they help stabilize voltage and filter signals.
2. **Industrial Applications**: In industrial settings, aluminum capacitors are used in power supplies, motor drives, and automation systems, where reliability is critical.
3. **Automotive Uses**: In the automotive industry, these capacitors are employed in various electronic control units (ECUs), infotainment systems, and safety features, ensuring optimal performance under varying conditions.
III. Importance of Product Standards
A. Ensuring Safety and Reliability
Product standards are vital for ensuring the safety and reliability of aluminum capacitors. They provide guidelines for manufacturers to follow, minimizing the risk of failures that could lead to hazardous situations, such as overheating or explosions.
B. Facilitating International Trade
Adhering to recognized product standards facilitates international trade by ensuring that products meet specific quality and safety requirements. This harmonization allows manufacturers to market their products globally without facing regulatory barriers.
C. Promoting Technological Advancement and Innovation
Standards encourage innovation by setting benchmarks for performance and quality. Manufacturers are motivated to improve their products to meet or exceed these standards, leading to advancements in technology and materials.
IV. Key Product Standards for Aluminum Capacitors
A. International Standards
1. **IEC (International Electrotechnical Commission)**: The IEC sets several standards for aluminum capacitors, including:
- **IEC 60384 Series**: This series covers fixed capacitors for use in electronic equipment, detailing performance requirements and testing methods.
- **IEC 61071**: This standard specifies the requirements for capacitors used in power electronics.
2. **ISO (International Organization for Standardization)**:
- **ISO 9001**: This standard focuses on quality management systems, ensuring that manufacturers maintain consistent quality in their production processes.
B. National Standards
1. **ANSI (American National Standards Institute)**: ANSI develops standards that ensure the safety and performance of aluminum capacitors in the United States.
2. **JIS (Japanese Industrial Standards)**: JIS provides guidelines for the manufacturing and testing of aluminum capacitors in Japan.
3. **GB (Guobiao Standards in China)**: GB standards govern the quality and safety of electronic components, including aluminum capacitors, in China.
C. Industry-Specific Standards
1. **Automotive Standards (e.g., AEC-Q200)**: This standard outlines the qualification requirements for passive components used in automotive applications, ensuring reliability under harsh conditions.
2. **Military Standards (e.g., MIL-PRF-39018)**: These standards specify the performance and reliability requirements for capacitors used in military applications, where failure is not an option.
V. Testing and Certification Processes
A. Overview of Testing Methods
To ensure compliance with product standards, aluminum capacitors undergo rigorous testing, including:
1. **Electrical Testing**: This includes measuring capacitance, equivalent series resistance (ESR), and leakage current to ensure the capacitor performs as expected.
2. **Environmental Testing**: Capacitors are subjected to various environmental conditions, such as temperature extremes, humidity, and vibration, to assess their durability and reliability.
B. Certification Bodies and Their Roles
Several certification bodies play a crucial role in the testing and certification of aluminum capacitors:
1. **UL (Underwriters Laboratories)**: UL provides safety certification for electronic components, ensuring they meet specific safety standards.
2. **TUV (Technischer Überwachungsverein)**: TUV offers testing and certification services, focusing on product safety and quality.
3. **CSA (Canadian Standards Association)**: CSA certifies products for compliance with Canadian safety standards, ensuring they are safe for use in the Canadian market.
VI. Compliance and Quality Assurance
A. Importance of Compliance with Standards
Compliance with product standards is essential for manufacturers to ensure their products are safe, reliable, and of high quality. Non-compliance can lead to product recalls, legal issues, and damage to a company's reputation.
B. Quality Assurance Processes in Manufacturing
Manufacturers implement various quality assurance processes to maintain compliance with standards:
1. **Incoming Material Inspection**: Raw materials are inspected upon arrival to ensure they meet specified quality standards.
2. **In-Process Quality Control**: Throughout the manufacturing process, quality control measures are implemented to monitor production and identify any deviations from standards.
3. **Final Product Testing**: Before products are shipped, they undergo final testing to verify that they meet all performance and safety requirements.
VII. Challenges in Meeting Product Standards
A. Technological Advancements and Evolving Standards
As technology evolves, so do product standards. Manufacturers must continuously adapt to new requirements, which can be challenging and resource-intensive.
B. Global Supply Chain Issues
Global supply chain disruptions can impact the availability of materials and components, making it difficult for manufacturers to meet standards consistently.
C. Balancing Cost and Compliance
Manufacturers often face the challenge of balancing the costs associated with compliance and quality assurance with the need to remain competitive in the market.
VIII. Future Trends in Aluminum Capacitor Standards
A. Innovations in Materials and Technology
The future of aluminum capacitors will likely see innovations in materials and technology, leading to improved performance and efficiency. New dielectric materials and manufacturing techniques may enhance capacitance and reduce size.
B. Increasing Focus on Sustainability and Environmental Impact
As environmental concerns grow, there will be an increasing focus on sustainability in the production of aluminum capacitors. Manufacturers may adopt eco-friendly materials and processes to minimize their environmental footprint.
C. Anticipated Changes in Regulatory Frameworks
Regulatory frameworks are expected to evolve, with stricter standards for safety and environmental impact. Manufacturers will need to stay informed and adapt to these changes to remain compliant.
IX. Conclusion
In conclusion, product standards for aluminum capacitors play a vital role in ensuring safety, reliability, and quality in electronic components. These standards facilitate international trade, promote technological advancement, and help manufacturers maintain compliance. As the industry evolves, staying abreast of key standards, testing processes, and future trends will be essential for manufacturers to succeed in a competitive market.
X. References
1. IEC 60384 Series - Fixed capacitors for use in electronic equipment.
2. ISO 9001 - Quality Management Systems.
3. AEC-Q200 - Qualification of passive components for automotive applications.
4. MIL-PRF-39018 - Military specification for capacitors.
5. UL, TUV, and CSA certification guidelines.
This comprehensive overview of product standards for aluminum capacitors highlights their significance in the electronics industry and provides insights into the future of these essential components.