Common Production Processes for Smart Capacitors
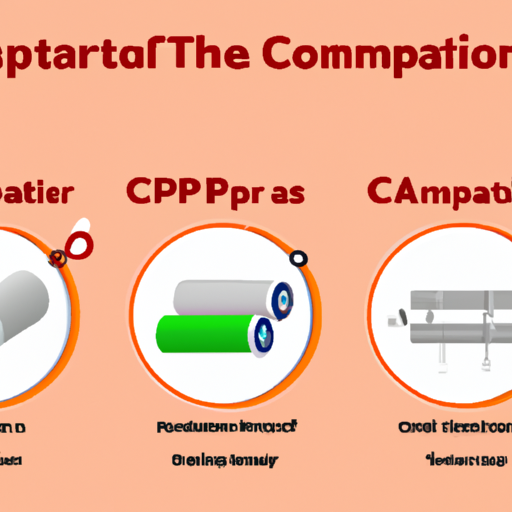
I. Introduction
In the rapidly evolving landscape of modern electronics, smart capacitors have emerged as pivotal components that enhance the performance and efficiency of various devices. These advanced capacitors not only store electrical energy but also incorporate intelligent features that allow them to adapt to changing conditions in real-time. This blog post will delve into the common production processes for smart capacitors, highlighting their significance, applications, and the intricate steps involved in their manufacturing.
II. Understanding Smart Capacitors
A. What are Smart Capacitors?
Smart capacitors are advanced energy storage devices that integrate traditional capacitor functionality with smart technology. Unlike conventional capacitors, which primarily serve to store and release electrical energy, smart capacitors can monitor and respond to electrical conditions, making them essential for applications requiring dynamic energy management.
B. Applications of Smart Capacitors
Smart capacitors find applications across various sectors, including:
1. **Power Electronics**: They are crucial in power conversion systems, enhancing efficiency and stability.
2. **Renewable Energy Systems**: Smart capacitors help manage energy flow in solar and wind power systems, optimizing performance.
3. **Electric Vehicles**: In EVs, they support energy recovery and management, improving overall efficiency.
4. **Consumer Electronics**: Smart capacitors enhance the performance of devices like smartphones and laptops by providing stable power supply and energy efficiency.
III. Overview of Production Processes
The production of smart capacitors involves several key stages, each critical to ensuring the final product meets the required specifications and performance standards. The general production flow includes:
1. **Design and Prototyping**
2. **Material Selection**
3. **Fabrication**
4. **Assembly**
5. **Testing and Quality Control**
IV. Detailed Production Processes
A. Design and Prototyping
The first step in producing smart capacitors is the design and prototyping phase. This involves:
1. **Computer-Aided Design (CAD) Tools**: Engineers use CAD software to create detailed designs of the capacitor, including its dimensions, materials, and electrical characteristics.
2. **Simulation and Modeling**: Before physical production, simulations are conducted to predict the performance of the capacitor under various conditions, allowing for optimization of the design.
3. **Prototyping Techniques**: Rapid prototyping methods, such as 3D printing, are employed to create initial models for testing and validation.
B. Material Selection
The choice of materials is crucial in determining the performance and reliability of smart capacitors. Key materials include:
1. **Dielectric Materials**: These materials, which insulate the capacitor and store electrical energy, must have high dielectric strength and low loss factors.
2. **Conductive Materials**: Conductors, such as metals or conductive polymers, are selected for their ability to efficiently transfer electrical energy.
3. **Substrate Materials**: The substrate provides structural support and must be compatible with the dielectric and conductive materials used.
C. Fabrication Techniques
The fabrication of smart capacitors involves several advanced techniques:
1. **Thin-Film Deposition**: This process involves depositing thin layers of materials onto a substrate to create the capacitor's structure. Two common methods are:
- **Physical Vapor Deposition (PVD)**: A vacuum process that involves vaporizing a solid material to form a thin film.
- **Chemical Vapor Deposition (CVD)**: A process that uses chemical reactions to produce thin films on the substrate.
2. **Screen Printing**: This technique is used to apply conductive inks onto substrates, forming the necessary electrical connections.
3. **Etching Processes**: Etching is employed to remove unwanted material and define patterns on the capacitor's surface.
4. **Laser Processing**: Lasers are used for precision cutting and structuring of materials, enhancing the capacitor's design and functionality.
D. Assembly Processes
Once the individual components are fabricated, they must be assembled. Key assembly processes include:
1. **Die Attach Techniques**: This involves attaching the capacitor die to the substrate using adhesives or soldering methods.
2. **Wire Bonding**: Fine wires are bonded to connect the capacitor's internal components to external leads, ensuring electrical connectivity.
3. **Encapsulation and Packaging**: The assembled capacitor is encapsulated to protect it from environmental factors and mechanical stress, followed by packaging for distribution.
E. Testing and Quality Control
Quality assurance is critical in capacitor production. The testing phase includes:
1. **Electrical Testing**: Capacitors are tested for capacitance, voltage rating, and leakage current to ensure they meet specifications.
2. **Environmental Testing**: Capacitors undergo tests to assess their performance under various environmental conditions, such as temperature and humidity.
3. **Reliability Testing**: Long-term reliability tests are conducted to evaluate the capacitor's performance over time, ensuring it can withstand operational stresses.
V. Innovations in Smart Capacitor Production
The production of smart capacitors is continually evolving, driven by innovations in materials science and manufacturing technologies. Key advancements include:
1. **Advances in Materials Science**: New dielectric and conductive materials are being developed to enhance performance and reduce costs.
2. **Automation and Industry 4.0**: The integration of automation and smart manufacturing technologies is streamlining production processes, improving efficiency and reducing human error.
3. **Sustainable Manufacturing Practices**: There is a growing emphasis on sustainability, with manufacturers adopting eco-friendly materials and processes to minimize environmental impact.
VI. Challenges in Smart Capacitor Production
Despite the advancements, several challenges persist in the production of smart capacitors:
1. **Cost Management**: The high cost of advanced materials and manufacturing processes can impact profitability.
2. **Supply Chain Issues**: Disruptions in the supply chain can lead to delays and increased costs in production.
3. **Technological Limitations**: The rapid pace of technological change can make it difficult for manufacturers to keep up with the latest advancements.
VII. Future Trends in Smart Capacitor Production
Looking ahead, several trends are expected to shape the future of smart capacitor production:
1. **Emerging Technologies**: Innovations such as nanotechnology and advanced composites are likely to enhance capacitor performance and reduce costs.
2. **Market Demand and Growth Projections**: The increasing demand for energy-efficient devices and renewable energy solutions is expected to drive growth in the smart capacitor market.
3. **Integration with IoT and Smart Grids**: As the Internet of Things (IoT) and smart grid technologies continue to expand, smart capacitors will play a crucial role in energy management and distribution.
VIII. Conclusion
Smart capacitors are integral to the advancement of modern electronics, offering enhanced performance and efficiency across various applications. Understanding the production processes involved in their manufacturing—from design and material selection to fabrication and testing—provides valuable insights into their significance in today's technology landscape. As innovations continue to emerge and challenges are addressed, the future of smart capacitor manufacturing looks promising, paving the way for even more advanced energy storage solutions.
IX. References
1. Academic Journals
2. Industry Reports
3. Relevant Books and Articles
This comprehensive overview of the common production processes for smart capacitors highlights their importance in modern electronics and the intricate steps involved in their manufacturing. As technology continues to evolve, smart capacitors will undoubtedly play a vital role in shaping the future of energy management and electronic devices.
Common Production Processes for Smart Capacitors
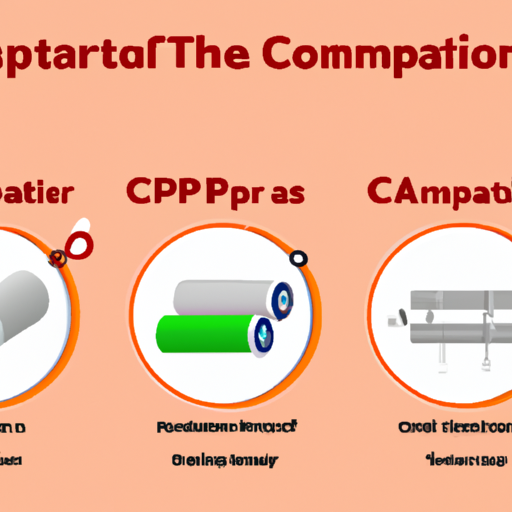
I. Introduction
In the rapidly evolving landscape of modern electronics, smart capacitors have emerged as pivotal components that enhance the performance and efficiency of various devices. These advanced capacitors not only store electrical energy but also incorporate intelligent features that allow them to adapt to changing conditions in real-time. This blog post will delve into the common production processes for smart capacitors, highlighting their significance, applications, and the intricate steps involved in their manufacturing.
II. Understanding Smart Capacitors
A. What are Smart Capacitors?
Smart capacitors are advanced energy storage devices that integrate traditional capacitor functionality with smart technology. Unlike conventional capacitors, which primarily serve to store and release electrical energy, smart capacitors can monitor and respond to electrical conditions, making them essential for applications requiring dynamic energy management.
B. Applications of Smart Capacitors
Smart capacitors find applications across various sectors, including:
1. **Power Electronics**: They are crucial in power conversion systems, enhancing efficiency and stability.
2. **Renewable Energy Systems**: Smart capacitors help manage energy flow in solar and wind power systems, optimizing performance.
3. **Electric Vehicles**: In EVs, they support energy recovery and management, improving overall efficiency.
4. **Consumer Electronics**: Smart capacitors enhance the performance of devices like smartphones and laptops by providing stable power supply and energy efficiency.
III. Overview of Production Processes
The production of smart capacitors involves several key stages, each critical to ensuring the final product meets the required specifications and performance standards. The general production flow includes:
1. **Design and Prototyping**
2. **Material Selection**
3. **Fabrication**
4. **Assembly**
5. **Testing and Quality Control**
IV. Detailed Production Processes
A. Design and Prototyping
The first step in producing smart capacitors is the design and prototyping phase. This involves:
1. **Computer-Aided Design (CAD) Tools**: Engineers use CAD software to create detailed designs of the capacitor, including its dimensions, materials, and electrical characteristics.
2. **Simulation and Modeling**: Before physical production, simulations are conducted to predict the performance of the capacitor under various conditions, allowing for optimization of the design.
3. **Prototyping Techniques**: Rapid prototyping methods, such as 3D printing, are employed to create initial models for testing and validation.
B. Material Selection
The choice of materials is crucial in determining the performance and reliability of smart capacitors. Key materials include:
1. **Dielectric Materials**: These materials, which insulate the capacitor and store electrical energy, must have high dielectric strength and low loss factors.
2. **Conductive Materials**: Conductors, such as metals or conductive polymers, are selected for their ability to efficiently transfer electrical energy.
3. **Substrate Materials**: The substrate provides structural support and must be compatible with the dielectric and conductive materials used.
C. Fabrication Techniques
The fabrication of smart capacitors involves several advanced techniques:
1. **Thin-Film Deposition**: This process involves depositing thin layers of materials onto a substrate to create the capacitor's structure. Two common methods are:
- **Physical Vapor Deposition (PVD)**: A vacuum process that involves vaporizing a solid material to form a thin film.
- **Chemical Vapor Deposition (CVD)**: A process that uses chemical reactions to produce thin films on the substrate.
2. **Screen Printing**: This technique is used to apply conductive inks onto substrates, forming the necessary electrical connections.
3. **Etching Processes**: Etching is employed to remove unwanted material and define patterns on the capacitor's surface.
4. **Laser Processing**: Lasers are used for precision cutting and structuring of materials, enhancing the capacitor's design and functionality.
D. Assembly Processes
Once the individual components are fabricated, they must be assembled. Key assembly processes include:
1. **Die Attach Techniques**: This involves attaching the capacitor die to the substrate using adhesives or soldering methods.
2. **Wire Bonding**: Fine wires are bonded to connect the capacitor's internal components to external leads, ensuring electrical connectivity.
3. **Encapsulation and Packaging**: The assembled capacitor is encapsulated to protect it from environmental factors and mechanical stress, followed by packaging for distribution.
E. Testing and Quality Control
Quality assurance is critical in capacitor production. The testing phase includes:
1. **Electrical Testing**: Capacitors are tested for capacitance, voltage rating, and leakage current to ensure they meet specifications.
2. **Environmental Testing**: Capacitors undergo tests to assess their performance under various environmental conditions, such as temperature and humidity.
3. **Reliability Testing**: Long-term reliability tests are conducted to evaluate the capacitor's performance over time, ensuring it can withstand operational stresses.
V. Innovations in Smart Capacitor Production
The production of smart capacitors is continually evolving, driven by innovations in materials science and manufacturing technologies. Key advancements include:
1. **Advances in Materials Science**: New dielectric and conductive materials are being developed to enhance performance and reduce costs.
2. **Automation and Industry 4.0**: The integration of automation and smart manufacturing technologies is streamlining production processes, improving efficiency and reducing human error.
3. **Sustainable Manufacturing Practices**: There is a growing emphasis on sustainability, with manufacturers adopting eco-friendly materials and processes to minimize environmental impact.
VI. Challenges in Smart Capacitor Production
Despite the advancements, several challenges persist in the production of smart capacitors:
1. **Cost Management**: The high cost of advanced materials and manufacturing processes can impact profitability.
2. **Supply Chain Issues**: Disruptions in the supply chain can lead to delays and increased costs in production.
3. **Technological Limitations**: The rapid pace of technological change can make it difficult for manufacturers to keep up with the latest advancements.
VII. Future Trends in Smart Capacitor Production
Looking ahead, several trends are expected to shape the future of smart capacitor production:
1. **Emerging Technologies**: Innovations such as nanotechnology and advanced composites are likely to enhance capacitor performance and reduce costs.
2. **Market Demand and Growth Projections**: The increasing demand for energy-efficient devices and renewable energy solutions is expected to drive growth in the smart capacitor market.
3. **Integration with IoT and Smart Grids**: As the Internet of Things (IoT) and smart grid technologies continue to expand, smart capacitors will play a crucial role in energy management and distribution.
VIII. Conclusion
Smart capacitors are integral to the advancement of modern electronics, offering enhanced performance and efficiency across various applications. Understanding the production processes involved in their manufacturing—from design and material selection to fabrication and testing—provides valuable insights into their significance in today's technology landscape. As innovations continue to emerge and challenges are addressed, the future of smart capacitor manufacturing looks promising, paving the way for even more advanced energy storage solutions.
IX. References
1. Academic Journals
2. Industry Reports
3. Relevant Books and Articles
This comprehensive overview of the common production processes for smart capacitors highlights their importance in modern electronics and the intricate steps involved in their manufacturing. As technology continues to evolve, smart capacitors will undoubtedly play a vital role in shaping the future of energy management and electronic devices.