Common Production Processes for Capacitors
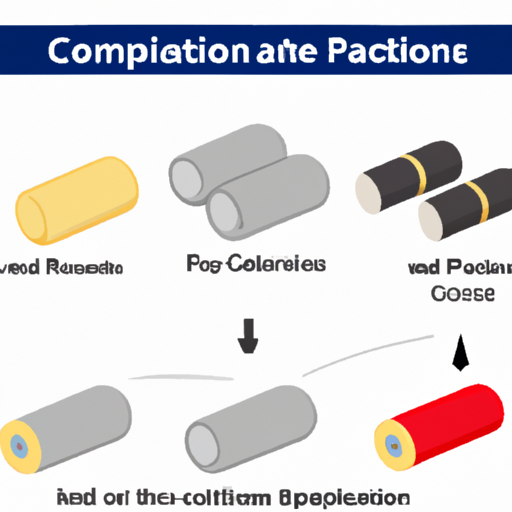
I. Introduction
Capacitors are essential components in modern electronic devices, serving as energy storage units that can release energy quickly when needed. They play a crucial role in various applications, from filtering signals in audio equipment to stabilizing voltage in power supplies. As technology advances, the demand for capacitors continues to grow, necessitating efficient and innovative production processes. This blog post will explore the common production processes for capacitors, delving into the types of capacitors, general production methods, specific processes for each type, and recent innovations in the field.
II. Types of Capacitors
Capacitors come in various types, each designed for specific applications and performance characteristics. The most common types include:
A. Ceramic Capacitors
Ceramic capacitors are widely used due to their small size, low cost, and stability. They are often found in high-frequency applications and are known for their reliability.
B. Electrolytic Capacitors
Electrolytic capacitors are polarized components that offer high capacitance values in a compact form. They are commonly used in power supply circuits and audio applications.
C. Film Capacitors
Film capacitors utilize a thin plastic film as the dielectric material. They are known for their excellent stability and low loss, making them suitable for high-frequency applications.
D. Tantalum Capacitors
Tantalum capacitors are known for their high capacitance and reliability. They are often used in applications where space is limited, such as in mobile devices.
E. Supercapacitors
Supercapacitors, or ultracapacitors, provide high energy storage and rapid charge/discharge capabilities. They are increasingly used in energy storage systems and hybrid vehicles.
III. General Production Processes
The production of capacitors involves several key processes, which can be broadly categorized into raw material selection, component fabrication, assembly, and testing.
A. Raw Material Selection
The first step in capacitor production is selecting the appropriate raw materials. This includes:
1. **Types of Materials Used**: Different capacitor types require specific materials. For instance, ceramic capacitors use ceramic powders, while electrolytic capacitors rely on aluminum or tantalum foils.
2. **Quality Control Measures**: Ensuring the quality of raw materials is critical. Manufacturers often conduct rigorous testing to verify the purity and properties of the materials before they are used in production.
B. Component Fabrication
Once the raw materials are selected, the next step is component fabrication, which includes:
1. **Dielectric Layer Preparation**: The dielectric material is prepared according to the specifications of the capacitor type. For ceramic capacitors, this involves mixing and processing ceramic powders.
2. **Electrode Production**: Electrodes are produced using various methods, such as sputtering or chemical deposition, depending on the capacitor type.
C. Assembly Process
The assembly process involves combining the fabricated components into a finished capacitor. This includes:
1. **Layer Stacking or Winding**: For capacitors like film and electrolytic types, layers of dielectric and electrodes are stacked or wound together to form the capacitor structure.
2. **Encapsulation Techniques**: The assembled capacitor is then encapsulated to protect it from environmental factors. This can involve using resin, plastic, or metal casings.
D. Testing and Quality Assurance
Quality assurance is a critical step in capacitor production. This includes:
1. **Electrical Testing**: Capacitors undergo electrical testing to ensure they meet specified capacitance, voltage, and leakage current standards.
2. **Environmental Testing**: Capacitors are subjected to environmental tests to assess their performance under various conditions, such as temperature and humidity.
3. **Reliability Testing**: Long-term reliability tests are conducted to ensure that capacitors can withstand operational stresses over time.
IV. Specific Production Processes by Capacitor Type
While the general production processes apply to all capacitors, each type has specific methods tailored to its unique characteristics.
A. Ceramic Capacitors
1. **Powder Preparation**: The production of ceramic capacitors begins with the preparation of ceramic powders, which are mixed with additives to achieve desired properties.
2. **Pressing and Sintering**: The mixed powders are pressed into desired shapes and then sintered at high temperatures to form a solid dielectric material.
3. **Electrode Application**: Electrodes are applied to the ceramic body, often using screen printing or sputtering techniques.
B. Electrolytic Capacitors
1. **Anode Foil Preparation**: The anode foil is prepared by etching aluminum or tantalum to increase its surface area, enhancing capacitance.
2. **Electrolyte Filling**: The capacitor is filled with an electrolyte solution, which is crucial for its operation.
3. **Sealing and Packaging**: After filling, the capacitor is sealed to prevent leakage and packaged for distribution.
C. Film Capacitors
1. **Film Extrusion**: The dielectric film is extruded from polymer materials, such as polyester or polypropylene.
2. **Metallization**: A thin layer of metal is deposited onto the film to form the electrodes, typically using vacuum deposition techniques.
3. **Winding and Cutting**: The metallized film is wound into a cylindrical shape and cut to the desired size.
D. Tantalum Capacitors
1. **Tantalum Powder Processing**: Tantalum powder is processed to create the anode, which is then formed into the desired shape.
2. **Anode Formation**: The anode undergoes an electrochemical process to form a dielectric layer on its surface.
3. **Encapsulation**: The finished anode is encapsulated in a protective casing to ensure reliability.
E. Supercapacitors
1. **Electrode Material Preparation**: Supercapacitors use materials like activated carbon for electrodes, which are prepared through various methods, including chemical activation.
2. **Assembly of Electrodes and Separators**: The electrodes are assembled with separators to prevent short circuits while allowing ionic movement.
3. **Electrolyte Filling**: The assembly is filled with an electrolyte, which is crucial for the capacitor's performance.
V. Innovations in Capacitor Production
The capacitor manufacturing industry is continually evolving, driven by advancements in technology and materials science. Some notable innovations include:
A. Advances in Materials Science
New materials are being developed to enhance capacitor performance, such as high-k dielectrics for ceramic capacitors and novel electrolytes for supercapacitors. These materials can improve energy density, stability, and efficiency.
B. Automation and Robotics in Manufacturing
Automation and robotics are increasingly being integrated into capacitor production lines. This not only increases efficiency and reduces labor costs but also enhances precision and consistency in manufacturing processes.
C. Environmental Considerations and Sustainability
Manufacturers are focusing on sustainable practices, such as reducing waste and energy consumption during production. The use of eco-friendly materials and recycling processes is becoming more common in the industry.
VI. Conclusion
In summary, the production processes for capacitors are complex and varied, reflecting the diverse types of capacitors available in the market. From raw material selection to testing and quality assurance, each step is crucial in ensuring the reliability and performance of capacitors in electronic devices. As technology continues to advance, the future of capacitor manufacturing looks promising, with ongoing research and development paving the way for innovative materials and processes. The importance of capacitors in modern electronics cannot be overstated, making their production a vital aspect of the electronics industry.
VII. References
1. Academic journals on capacitor technology and materials science.
2. Industry reports detailing trends and innovations in capacitor manufacturing.
3. Manufacturer guidelines and specifications for various types of capacitors.
This comprehensive overview of capacitor production processes highlights the intricate steps involved in creating these essential components, emphasizing the importance of quality and innovation in the industry.
Common Production Processes for Capacitors
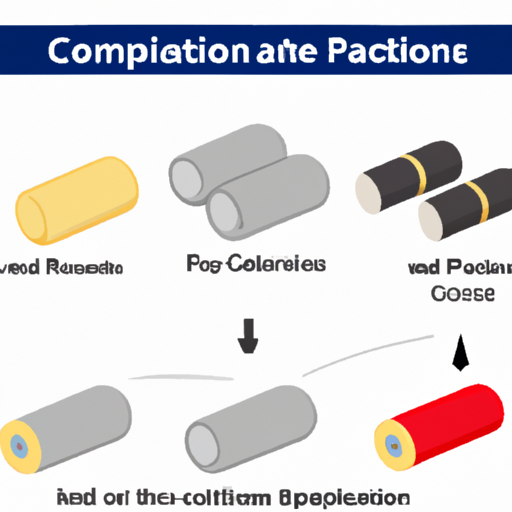
I. Introduction
Capacitors are essential components in modern electronic devices, serving as energy storage units that can release energy quickly when needed. They play a crucial role in various applications, from filtering signals in audio equipment to stabilizing voltage in power supplies. As technology advances, the demand for capacitors continues to grow, necessitating efficient and innovative production processes. This blog post will explore the common production processes for capacitors, delving into the types of capacitors, general production methods, specific processes for each type, and recent innovations in the field.
II. Types of Capacitors
Capacitors come in various types, each designed for specific applications and performance characteristics. The most common types include:
A. Ceramic Capacitors
Ceramic capacitors are widely used due to their small size, low cost, and stability. They are often found in high-frequency applications and are known for their reliability.
B. Electrolytic Capacitors
Electrolytic capacitors are polarized components that offer high capacitance values in a compact form. They are commonly used in power supply circuits and audio applications.
C. Film Capacitors
Film capacitors utilize a thin plastic film as the dielectric material. They are known for their excellent stability and low loss, making them suitable for high-frequency applications.
D. Tantalum Capacitors
Tantalum capacitors are known for their high capacitance and reliability. They are often used in applications where space is limited, such as in mobile devices.
E. Supercapacitors
Supercapacitors, or ultracapacitors, provide high energy storage and rapid charge/discharge capabilities. They are increasingly used in energy storage systems and hybrid vehicles.
III. General Production Processes
The production of capacitors involves several key processes, which can be broadly categorized into raw material selection, component fabrication, assembly, and testing.
A. Raw Material Selection
The first step in capacitor production is selecting the appropriate raw materials. This includes:
1. **Types of Materials Used**: Different capacitor types require specific materials. For instance, ceramic capacitors use ceramic powders, while electrolytic capacitors rely on aluminum or tantalum foils.
2. **Quality Control Measures**: Ensuring the quality of raw materials is critical. Manufacturers often conduct rigorous testing to verify the purity and properties of the materials before they are used in production.
B. Component Fabrication
Once the raw materials are selected, the next step is component fabrication, which includes:
1. **Dielectric Layer Preparation**: The dielectric material is prepared according to the specifications of the capacitor type. For ceramic capacitors, this involves mixing and processing ceramic powders.
2. **Electrode Production**: Electrodes are produced using various methods, such as sputtering or chemical deposition, depending on the capacitor type.
C. Assembly Process
The assembly process involves combining the fabricated components into a finished capacitor. This includes:
1. **Layer Stacking or Winding**: For capacitors like film and electrolytic types, layers of dielectric and electrodes are stacked or wound together to form the capacitor structure.
2. **Encapsulation Techniques**: The assembled capacitor is then encapsulated to protect it from environmental factors. This can involve using resin, plastic, or metal casings.
D. Testing and Quality Assurance
Quality assurance is a critical step in capacitor production. This includes:
1. **Electrical Testing**: Capacitors undergo electrical testing to ensure they meet specified capacitance, voltage, and leakage current standards.
2. **Environmental Testing**: Capacitors are subjected to environmental tests to assess their performance under various conditions, such as temperature and humidity.
3. **Reliability Testing**: Long-term reliability tests are conducted to ensure that capacitors can withstand operational stresses over time.
IV. Specific Production Processes by Capacitor Type
While the general production processes apply to all capacitors, each type has specific methods tailored to its unique characteristics.
A. Ceramic Capacitors
1. **Powder Preparation**: The production of ceramic capacitors begins with the preparation of ceramic powders, which are mixed with additives to achieve desired properties.
2. **Pressing and Sintering**: The mixed powders are pressed into desired shapes and then sintered at high temperatures to form a solid dielectric material.
3. **Electrode Application**: Electrodes are applied to the ceramic body, often using screen printing or sputtering techniques.
B. Electrolytic Capacitors
1. **Anode Foil Preparation**: The anode foil is prepared by etching aluminum or tantalum to increase its surface area, enhancing capacitance.
2. **Electrolyte Filling**: The capacitor is filled with an electrolyte solution, which is crucial for its operation.
3. **Sealing and Packaging**: After filling, the capacitor is sealed to prevent leakage and packaged for distribution.
C. Film Capacitors
1. **Film Extrusion**: The dielectric film is extruded from polymer materials, such as polyester or polypropylene.
2. **Metallization**: A thin layer of metal is deposited onto the film to form the electrodes, typically using vacuum deposition techniques.
3. **Winding and Cutting**: The metallized film is wound into a cylindrical shape and cut to the desired size.
D. Tantalum Capacitors
1. **Tantalum Powder Processing**: Tantalum powder is processed to create the anode, which is then formed into the desired shape.
2. **Anode Formation**: The anode undergoes an electrochemical process to form a dielectric layer on its surface.
3. **Encapsulation**: The finished anode is encapsulated in a protective casing to ensure reliability.
E. Supercapacitors
1. **Electrode Material Preparation**: Supercapacitors use materials like activated carbon for electrodes, which are prepared through various methods, including chemical activation.
2. **Assembly of Electrodes and Separators**: The electrodes are assembled with separators to prevent short circuits while allowing ionic movement.
3. **Electrolyte Filling**: The assembly is filled with an electrolyte, which is crucial for the capacitor's performance.
V. Innovations in Capacitor Production
The capacitor manufacturing industry is continually evolving, driven by advancements in technology and materials science. Some notable innovations include:
A. Advances in Materials Science
New materials are being developed to enhance capacitor performance, such as high-k dielectrics for ceramic capacitors and novel electrolytes for supercapacitors. These materials can improve energy density, stability, and efficiency.
B. Automation and Robotics in Manufacturing
Automation and robotics are increasingly being integrated into capacitor production lines. This not only increases efficiency and reduces labor costs but also enhances precision and consistency in manufacturing processes.
C. Environmental Considerations and Sustainability
Manufacturers are focusing on sustainable practices, such as reducing waste and energy consumption during production. The use of eco-friendly materials and recycling processes is becoming more common in the industry.
VI. Conclusion
In summary, the production processes for capacitors are complex and varied, reflecting the diverse types of capacitors available in the market. From raw material selection to testing and quality assurance, each step is crucial in ensuring the reliability and performance of capacitors in electronic devices. As technology continues to advance, the future of capacitor manufacturing looks promising, with ongoing research and development paving the way for innovative materials and processes. The importance of capacitors in modern electronics cannot be overstated, making their production a vital aspect of the electronics industry.
VII. References
1. Academic journals on capacitor technology and materials science.
2. Industry reports detailing trends and innovations in capacitor manufacturing.
3. Manufacturer guidelines and specifications for various types of capacitors.
This comprehensive overview of capacitor production processes highlights the intricate steps involved in creating these essential components, emphasizing the importance of quality and innovation in the industry.