What is the Mainstream Pulse Capacitor Production Process?
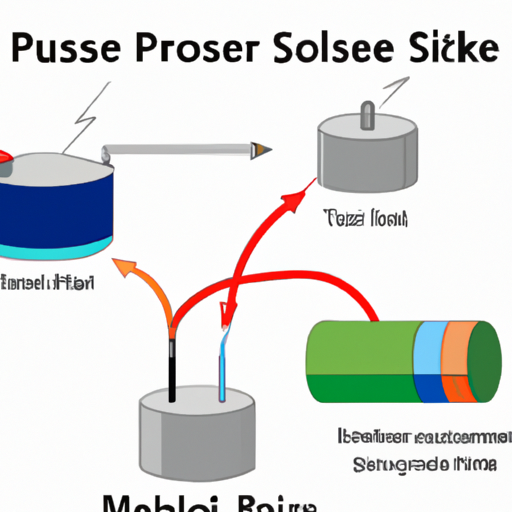
I. Introduction
A. Definition of Pulse Capacitors
Pulse capacitors are specialized capacitors designed to handle high-energy pulses of electricity. Unlike standard capacitors, which are typically used for smoothing and filtering applications, pulse capacitors are engineered to deliver quick bursts of energy, making them essential components in various high-performance applications.
B. Importance of Pulse Capacitors in Various Applications
The significance of pulse capacitors cannot be overstated. They play a crucial role in power electronics, medical devices, and telecommunications, where rapid energy discharge is necessary. For instance, in medical devices like defibrillators, pulse capacitors provide the necessary energy to deliver life-saving shocks. In telecommunications, they help manage power surges, ensuring reliable communication.
C. Overview of the Production Process
The production of pulse capacitors involves a series of intricate steps, from material selection to final testing. This blog post will explore the mainstream production process, highlighting the materials used, the assembly techniques, and the challenges faced by manufacturers.
II. Understanding Pulse Capacitors
A. Types of Pulse Capacitors
1. **Film Capacitors**: These capacitors use thin plastic films as dielectric materials. They are known for their stability and low loss, making them suitable for high-frequency applications.
2. **Ceramic Capacitors**: Utilizing ceramic materials as dielectrics, these capacitors are compact and can handle high voltages. They are often used in RF applications and power electronics.
3. **Electrolytic Capacitors**: These capacitors use an electrolyte as one of their plates, allowing for higher capacitance values. They are commonly found in power supply circuits.
B. Key Characteristics and Specifications
1. **Voltage Rating**: This indicates the maximum voltage the capacitor can handle without breaking down. Pulse capacitors are designed to withstand high voltage spikes.
2. **Capacitance Value**: This measures the capacitor's ability to store charge. Pulse capacitors typically have lower capacitance values compared to standard capacitors but are optimized for rapid discharge.
3. **Ripple Current Rating**: This specification indicates the maximum AC current the capacitor can handle without overheating, which is critical in pulse applications.
C. Applications of Pulse Capacitors
1. **Power Electronics**: Inverters and converters rely on pulse capacitors to manage energy flow efficiently.
2. **Medical Devices**: Devices like defibrillators and pacemakers utilize pulse capacitors for their rapid energy discharge capabilities.
3. **Telecommunications**: Pulse capacitors help in managing power surges and ensuring signal integrity in communication systems.
III. Raw Materials for Pulse Capacitors
A. Dielectric Materials
1. **Polypropylene**: Known for its excellent electrical properties and stability, polypropylene is a common choice for film capacitors.
2. **Polyester**: This material is used for its cost-effectiveness and decent performance in various applications.
3. **Ceramic Materials**: These are used in high-voltage applications due to their ability to withstand extreme conditions.
B. Conductive Materials
1. **Aluminum Foil**: Often used as one of the plates in capacitors, aluminum foil is favored for its conductivity and lightweight properties.
2. **Copper**: Copper is used in applications requiring high conductivity and is often found in the terminals of capacitors.
C. Insulating Materials
1. **Epoxy Resins**: These are used for encapsulating capacitors, providing mechanical strength and environmental protection.
2. **Polyimide Films**: Known for their thermal stability, polyimide films are used in high-temperature applications.
IV. The Production Process of Pulse Capacitors
A. Design and Engineering
1. **Specifications and Requirements**: The production process begins with defining the specifications based on the intended application. This includes voltage ratings, capacitance values, and physical dimensions.
2. **Simulation and Prototyping**: Engineers use simulation software to model the capacitor's performance under various conditions. Prototyping allows for testing and refinement before mass production.
B. Material Preparation
1. **Sourcing and Quality Control**: Raw materials are sourced from reliable suppliers, and quality control measures are implemented to ensure they meet industry standards.
2. **Cutting and Shaping Dielectric and Conductive Materials**: The dielectric and conductive materials are cut and shaped to the required dimensions, ensuring precision for optimal performance.
C. Assembly Process
1. **Layering of Dielectric and Conductive Materials**: The assembly begins with layering the dielectric material between the conductive plates. This is crucial for the capacitor's performance.
2. **Winding or Stacking Techniques**: Depending on the type of capacitor, the layers may be wound into a cylindrical shape or stacked in a rectangular configuration.
3. **Connection of Terminals**: The conductive plates are connected to terminals, which will later be used for electrical connections in circuits.
D. Encapsulation and Insulation
1. **Application of Insulating Materials**: Insulating materials are applied to protect the capacitor from environmental factors and to ensure safety during operation.
2. **Curing and Hardening Processes**: The encapsulated capacitors undergo curing processes to harden the insulating materials, providing durability and reliability.
E. Testing and Quality Assurance
1. **Electrical Testing**: Each capacitor is subjected to electrical testing to verify its performance against specified ratings.
2. **Mechanical Testing**: Mechanical tests ensure that the capacitors can withstand physical stresses during operation.
3. **Environmental Testing**: Capacitors are tested under various environmental conditions to ensure they can perform reliably in real-world applications.
V. Challenges in Pulse Capacitor Production
A. Material Limitations
The choice of materials can significantly impact the performance and cost of pulse capacitors. Manufacturers must balance performance with availability and cost-effectiveness.
B. Precision and Tolerance Issues
The production of pulse capacitors requires high precision. Any deviation in dimensions can lead to performance issues, making strict quality control essential.
C. Cost Management
As with many manufacturing processes, managing costs while maintaining quality is a constant challenge. Manufacturers must find ways to optimize production without compromising performance.
D. Environmental Considerations
With increasing awareness of environmental issues, manufacturers are under pressure to adopt sustainable practices in the production of pulse capacitors, including recycling materials and reducing waste.
VI. Innovations and Future Trends
A. Advances in Materials Science
Research into new materials is ongoing, with a focus on developing dielectrics that can handle higher voltages and temperatures while being more environmentally friendly.
B. Automation and Smart Manufacturing
The integration of automation in the production process is enhancing efficiency and precision, allowing for faster production times and reduced labor costs.
C. Sustainability in Production
Manufacturers are increasingly adopting sustainable practices, such as using recyclable materials and reducing energy consumption during production.
D. Emerging Applications and Markets
As technology evolves, new applications for pulse capacitors are emerging, particularly in renewable energy systems and electric vehicles, where rapid energy discharge is critical.
VII. Conclusion
A. Recap of the Pulse Capacitor Production Process
The production of pulse capacitors is a complex process that involves careful material selection, precise engineering, and rigorous testing. Each step is crucial to ensure the final product meets the high-performance standards required in various applications.
B. The Role of Pulse Capacitors in Modern Technology
Pulse capacitors are integral to many modern technologies, enabling advancements in power electronics, medical devices, and telecommunications. Their ability to deliver rapid bursts of energy makes them indispensable in high-performance applications.
C. Future Outlook for the Industry
As technology continues to advance, the demand for pulse capacitors is expected to grow. Innovations in materials and manufacturing processes will likely lead to even more efficient and reliable capacitors, further solidifying their role in modern technology.
VIII. References
A. Academic Journals
- Journal of Electrical Engineering
- IEEE Transactions on Power Electronics
B. Industry Reports
- Market Research Reports on Capacitor Technologies
- Industry Analysis on Pulse Capacitor Applications
C. Manufacturer Guidelines
- Technical Specifications from Leading Capacitor Manufacturers
- Best Practices in Capacitor Production
---
This blog post provides a comprehensive overview of the mainstream pulse capacitor production process, highlighting its significance in modern technology and the challenges faced by manufacturers. As the industry evolves, staying informed about innovations and trends will be crucial for those involved in the field.
What is the Mainstream Pulse Capacitor Production Process?
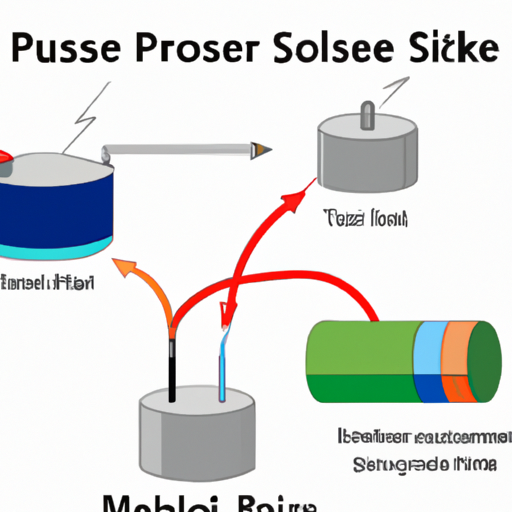
I. Introduction
A. Definition of Pulse Capacitors
Pulse capacitors are specialized capacitors designed to handle high-energy pulses of electricity. Unlike standard capacitors, which are typically used for smoothing and filtering applications, pulse capacitors are engineered to deliver quick bursts of energy, making them essential components in various high-performance applications.
B. Importance of Pulse Capacitors in Various Applications
The significance of pulse capacitors cannot be overstated. They play a crucial role in power electronics, medical devices, and telecommunications, where rapid energy discharge is necessary. For instance, in medical devices like defibrillators, pulse capacitors provide the necessary energy to deliver life-saving shocks. In telecommunications, they help manage power surges, ensuring reliable communication.
C. Overview of the Production Process
The production of pulse capacitors involves a series of intricate steps, from material selection to final testing. This blog post will explore the mainstream production process, highlighting the materials used, the assembly techniques, and the challenges faced by manufacturers.
II. Understanding Pulse Capacitors
A. Types of Pulse Capacitors
1. **Film Capacitors**: These capacitors use thin plastic films as dielectric materials. They are known for their stability and low loss, making them suitable for high-frequency applications.
2. **Ceramic Capacitors**: Utilizing ceramic materials as dielectrics, these capacitors are compact and can handle high voltages. They are often used in RF applications and power electronics.
3. **Electrolytic Capacitors**: These capacitors use an electrolyte as one of their plates, allowing for higher capacitance values. They are commonly found in power supply circuits.
B. Key Characteristics and Specifications
1. **Voltage Rating**: This indicates the maximum voltage the capacitor can handle without breaking down. Pulse capacitors are designed to withstand high voltage spikes.
2. **Capacitance Value**: This measures the capacitor's ability to store charge. Pulse capacitors typically have lower capacitance values compared to standard capacitors but are optimized for rapid discharge.
3. **Ripple Current Rating**: This specification indicates the maximum AC current the capacitor can handle without overheating, which is critical in pulse applications.
C. Applications of Pulse Capacitors
1. **Power Electronics**: Inverters and converters rely on pulse capacitors to manage energy flow efficiently.
2. **Medical Devices**: Devices like defibrillators and pacemakers utilize pulse capacitors for their rapid energy discharge capabilities.
3. **Telecommunications**: Pulse capacitors help in managing power surges and ensuring signal integrity in communication systems.
III. Raw Materials for Pulse Capacitors
A. Dielectric Materials
1. **Polypropylene**: Known for its excellent electrical properties and stability, polypropylene is a common choice for film capacitors.
2. **Polyester**: This material is used for its cost-effectiveness and decent performance in various applications.
3. **Ceramic Materials**: These are used in high-voltage applications due to their ability to withstand extreme conditions.
B. Conductive Materials
1. **Aluminum Foil**: Often used as one of the plates in capacitors, aluminum foil is favored for its conductivity and lightweight properties.
2. **Copper**: Copper is used in applications requiring high conductivity and is often found in the terminals of capacitors.
C. Insulating Materials
1. **Epoxy Resins**: These are used for encapsulating capacitors, providing mechanical strength and environmental protection.
2. **Polyimide Films**: Known for their thermal stability, polyimide films are used in high-temperature applications.
IV. The Production Process of Pulse Capacitors
A. Design and Engineering
1. **Specifications and Requirements**: The production process begins with defining the specifications based on the intended application. This includes voltage ratings, capacitance values, and physical dimensions.
2. **Simulation and Prototyping**: Engineers use simulation software to model the capacitor's performance under various conditions. Prototyping allows for testing and refinement before mass production.
B. Material Preparation
1. **Sourcing and Quality Control**: Raw materials are sourced from reliable suppliers, and quality control measures are implemented to ensure they meet industry standards.
2. **Cutting and Shaping Dielectric and Conductive Materials**: The dielectric and conductive materials are cut and shaped to the required dimensions, ensuring precision for optimal performance.
C. Assembly Process
1. **Layering of Dielectric and Conductive Materials**: The assembly begins with layering the dielectric material between the conductive plates. This is crucial for the capacitor's performance.
2. **Winding or Stacking Techniques**: Depending on the type of capacitor, the layers may be wound into a cylindrical shape or stacked in a rectangular configuration.
3. **Connection of Terminals**: The conductive plates are connected to terminals, which will later be used for electrical connections in circuits.
D. Encapsulation and Insulation
1. **Application of Insulating Materials**: Insulating materials are applied to protect the capacitor from environmental factors and to ensure safety during operation.
2. **Curing and Hardening Processes**: The encapsulated capacitors undergo curing processes to harden the insulating materials, providing durability and reliability.
E. Testing and Quality Assurance
1. **Electrical Testing**: Each capacitor is subjected to electrical testing to verify its performance against specified ratings.
2. **Mechanical Testing**: Mechanical tests ensure that the capacitors can withstand physical stresses during operation.
3. **Environmental Testing**: Capacitors are tested under various environmental conditions to ensure they can perform reliably in real-world applications.
V. Challenges in Pulse Capacitor Production
A. Material Limitations
The choice of materials can significantly impact the performance and cost of pulse capacitors. Manufacturers must balance performance with availability and cost-effectiveness.
B. Precision and Tolerance Issues
The production of pulse capacitors requires high precision. Any deviation in dimensions can lead to performance issues, making strict quality control essential.
C. Cost Management
As with many manufacturing processes, managing costs while maintaining quality is a constant challenge. Manufacturers must find ways to optimize production without compromising performance.
D. Environmental Considerations
With increasing awareness of environmental issues, manufacturers are under pressure to adopt sustainable practices in the production of pulse capacitors, including recycling materials and reducing waste.
VI. Innovations and Future Trends
A. Advances in Materials Science
Research into new materials is ongoing, with a focus on developing dielectrics that can handle higher voltages and temperatures while being more environmentally friendly.
B. Automation and Smart Manufacturing
The integration of automation in the production process is enhancing efficiency and precision, allowing for faster production times and reduced labor costs.
C. Sustainability in Production
Manufacturers are increasingly adopting sustainable practices, such as using recyclable materials and reducing energy consumption during production.
D. Emerging Applications and Markets
As technology evolves, new applications for pulse capacitors are emerging, particularly in renewable energy systems and electric vehicles, where rapid energy discharge is critical.
VII. Conclusion
A. Recap of the Pulse Capacitor Production Process
The production of pulse capacitors is a complex process that involves careful material selection, precise engineering, and rigorous testing. Each step is crucial to ensure the final product meets the high-performance standards required in various applications.
B. The Role of Pulse Capacitors in Modern Technology
Pulse capacitors are integral to many modern technologies, enabling advancements in power electronics, medical devices, and telecommunications. Their ability to deliver rapid bursts of energy makes them indispensable in high-performance applications.
C. Future Outlook for the Industry
As technology continues to advance, the demand for pulse capacitors is expected to grow. Innovations in materials and manufacturing processes will likely lead to even more efficient and reliable capacitors, further solidifying their role in modern technology.
VIII. References
A. Academic Journals
- Journal of Electrical Engineering
- IEEE Transactions on Power Electronics
B. Industry Reports
- Market Research Reports on Capacitor Technologies
- Industry Analysis on Pulse Capacitor Applications
C. Manufacturer Guidelines
- Technical Specifications from Leading Capacitor Manufacturers
- Best Practices in Capacitor Production
---
This blog post provides a comprehensive overview of the mainstream pulse capacitor production process, highlighting its significance in modern technology and the challenges faced by manufacturers. As the industry evolves, staying informed about innovations and trends will be crucial for those involved in the field.