What is the Mainstream Production Process of Parallel Capacitors?
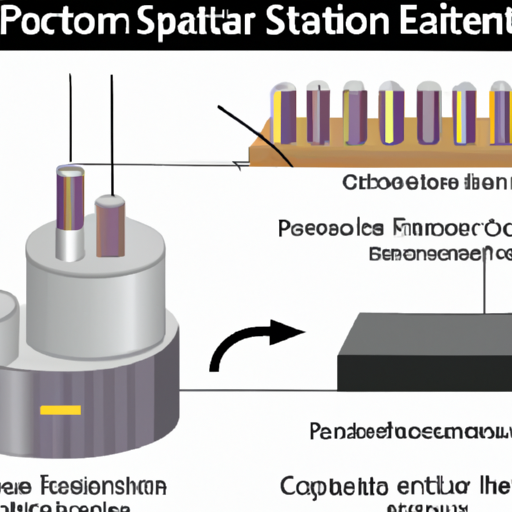
I. Introduction
A. Definition of Parallel Capacitors
Parallel capacitors are capacitors connected in such a way that they share the same voltage across their terminals. This configuration allows for the total capacitance to be the sum of the individual capacitances, enhancing the overall capacitance in electronic circuits. This is particularly useful in applications where higher capacitance values are required without increasing the voltage rating.
B. Importance of Capacitors in Electronic Circuits
Capacitors play a crucial role in electronic circuits, serving various functions such as energy storage, filtering, and signal coupling. They are essential components in power supply circuits, audio equipment, and timing applications. The ability to combine multiple capacitors in parallel allows designers to optimize circuit performance, manage power distribution, and improve signal integrity.
C. Overview of the Production Process
The production of parallel capacitors involves a series of well-defined steps, from material selection to final assembly and testing. Understanding this process is vital for manufacturers aiming to produce high-quality capacitors that meet industry standards and customer expectations.
II. Types of Parallel Capacitors
A. Ceramic Capacitors
Ceramic capacitors are widely used due to their small size, low cost, and excellent stability. They are made from ceramic materials that serve as dielectrics, providing reliable performance in various applications.
B. Electrolytic Capacitors
Electrolytic capacitors are polarized capacitors that offer high capacitance values in a compact form. They are commonly used in power supply circuits and audio applications, where large capacitance is needed.
C. Film Capacitors
Film capacitors utilize thin plastic films as dielectrics. They are known for their stability, low loss, and high insulation resistance, making them suitable for high-frequency applications.
D. Tantalum Capacitors
Tantalum capacitors are known for their high capacitance-to-volume ratio and reliability. They are often used in applications where space is limited, such as in mobile devices and aerospace electronics.
E. Comparison of Different Types
Each type of capacitor has its advantages and disadvantages, making them suitable for specific applications. For instance, while ceramic capacitors are ideal for high-frequency applications, electrolytic capacitors are preferred for power supply circuits due to their high capacitance.
III. Raw Materials Used in Capacitor Production
A. Dielectric Materials
1. Types of Dielectrics
The dielectric material is a critical component of capacitors, influencing their performance. Common dielectric materials include ceramic, polyester, polypropylene, and tantalum oxide.
2. Properties Required for Dielectrics
Dielectrics must possess high insulation resistance, low dielectric loss, and stability over a range of temperatures and frequencies. These properties ensure that capacitors function effectively in various environments.
B. Conductive Materials
1. Metals Used (e.g., Aluminum, Tantalum)
Conductive materials, such as aluminum and tantalum, are used for the electrodes in capacitors. These metals are chosen for their excellent conductivity and compatibility with dielectric materials.
2. Conductive Coatings
In some capacitor designs, conductive coatings are applied to enhance conductivity and improve performance. These coatings can be made from various materials, including silver and copper.
C. Packaging Materials
1. Types of Packaging
Packaging materials protect capacitors from environmental factors and mechanical stress. Common packaging types include plastic, metal cans, and ceramic enclosures.
2. Importance of Packaging in Capacitor Performance
Proper packaging is essential for maintaining the integrity and performance of capacitors. It prevents moisture ingress, physical damage, and ensures reliable operation in various applications.
IV. The Production Process
A. Design and Engineering
1. Specifications and Requirements
The production process begins with design and engineering, where specifications for the capacitors are established. This includes determining capacitance values, voltage ratings, and physical dimensions.
2. Prototyping and Testing
Prototyping is a crucial step that allows manufacturers to test designs and make necessary adjustments before mass production. This phase often involves rigorous testing to ensure that the capacitors meet performance standards.
B. Material Preparation
1. Sourcing and Quality Control
Raw materials are sourced from suppliers, and quality control measures are implemented to ensure that they meet the required specifications. This step is vital for maintaining the overall quality of the final product.
2. Material Processing Techniques
Materials undergo various processing techniques, such as cutting, layering, and coating, to prepare them for assembly. These techniques are tailored to the specific type of capacitor being produced.
C. Manufacturing Steps
1. Layering and Assembly
a. Dielectric Layering
The dielectric material is layered according to the design specifications. This step is critical for determining the capacitor's performance characteristics.
b. Electrode Placement
Electrodes are then placed on the dielectric layers, ensuring proper alignment and contact. This step is essential for achieving the desired capacitance.
2. Encapsulation
a. Methods of Encapsulation
Encapsulation protects the internal components of the capacitor from environmental factors. Various methods, such as resin coating and heat-shrink tubing, are used depending on the capacitor type.
b. Importance of Encapsulation
Encapsulation is crucial for ensuring the longevity and reliability of capacitors, especially in harsh environments.
3. Electrical Testing
a. Testing Procedures
Once assembled, capacitors undergo electrical testing to verify their performance. This includes measuring capacitance, leakage current, and equivalent series resistance (ESR).
b. Quality Assurance
Quality assurance measures are implemented to ensure that only capacitors meeting the required specifications are released for distribution.
D. Final Assembly and Packaging
1. Final Inspection
Before packaging, capacitors undergo a final inspection to check for defects and ensure compliance with quality standards.
2. Packaging for Distribution
Capacitors are then packaged for distribution, ensuring that they are protected during transportation and storage.
V. Quality Control Measures
A. In-Process Quality Control
In-process quality control measures are implemented throughout the production process to identify and address issues early, ensuring consistent quality.
B. End-of-Line Testing
End-of-line testing is conducted on finished products to verify that they meet performance specifications before being shipped to customers.
C. Compliance with Industry Standards
1. ISO Standards
Manufacturers often adhere to ISO standards to ensure quality management and continuous improvement in their production processes.
2. RoHS Compliance
Compliance with RoHS (Restriction of Hazardous Substances) regulations is essential for ensuring that capacitors are free from harmful materials, promoting environmental sustainability.
VI. Challenges in Capacitor Production
A. Material Sourcing Issues
Sourcing high-quality materials can be challenging, especially with fluctuating market prices and availability of raw materials.
B. Technological Advancements
Keeping up with technological advancements in capacitor design and manufacturing processes is essential for maintaining competitiveness in the market.
C. Environmental Considerations
Manufacturers must address environmental concerns related to waste management and the use of hazardous materials in capacitor production.
D. Market Demand Fluctuations
Market demand for capacitors can fluctuate, impacting production schedules and inventory management.
VII. Future Trends in Capacitor Production
A. Innovations in Materials
Research into new dielectric and conductive materials is ongoing, with the aim of improving capacitor performance and reducing costs.
B. Advances in Manufacturing Techniques
Advancements in manufacturing techniques, such as automation and additive manufacturing, are expected to enhance production efficiency and reduce waste.
C. Sustainability Practices
Sustainability practices are becoming increasingly important, with manufacturers seeking to minimize their environmental impact through eco-friendly materials and processes.
D. Impact of Emerging Technologies (e.g., Electric Vehicles, Renewable Energy)
The rise of electric vehicles and renewable energy technologies is driving demand for high-performance capacitors, leading to innovations in design and production.
VIII. Conclusion
A. Summary of the Production Process
The production process of parallel capacitors involves a series of well-defined steps, from material selection to final assembly and testing. Each stage is critical for ensuring the quality and performance of the final product.
B. Importance of Continuous Improvement in Manufacturing
Continuous improvement in manufacturing processes is essential for meeting the evolving demands of the electronics industry and maintaining competitiveness.
C. Future Outlook for Parallel Capacitors in Electronics
As technology continues to advance, the demand for high-quality parallel capacitors will only increase. Manufacturers must adapt to these changes, embracing innovation and sustainability to thrive in the future.
IX. References
A. Academic Journals
B. Industry Reports
C. Manufacturer Guidelines
D. Standards Organizations
This blog post provides a comprehensive overview of the mainstream production process of parallel capacitors, highlighting the importance of each step and the challenges faced by manufacturers. By understanding this process, readers can appreciate the complexity and significance of capacitors in modern electronics.
What is the Mainstream Production Process of Parallel Capacitors?
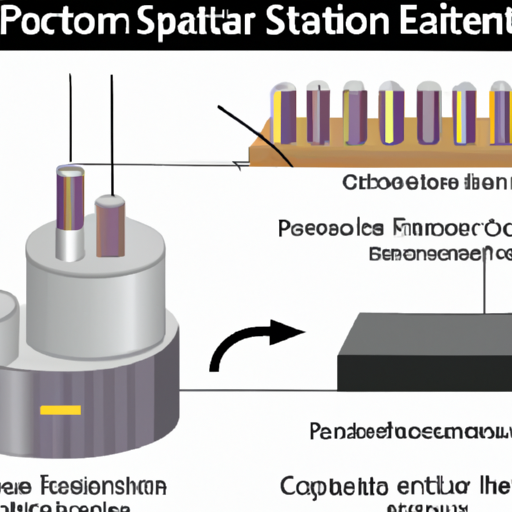
I. Introduction
A. Definition of Parallel Capacitors
Parallel capacitors are capacitors connected in such a way that they share the same voltage across their terminals. This configuration allows for the total capacitance to be the sum of the individual capacitances, enhancing the overall capacitance in electronic circuits. This is particularly useful in applications where higher capacitance values are required without increasing the voltage rating.
B. Importance of Capacitors in Electronic Circuits
Capacitors play a crucial role in electronic circuits, serving various functions such as energy storage, filtering, and signal coupling. They are essential components in power supply circuits, audio equipment, and timing applications. The ability to combine multiple capacitors in parallel allows designers to optimize circuit performance, manage power distribution, and improve signal integrity.
C. Overview of the Production Process
The production of parallel capacitors involves a series of well-defined steps, from material selection to final assembly and testing. Understanding this process is vital for manufacturers aiming to produce high-quality capacitors that meet industry standards and customer expectations.
II. Types of Parallel Capacitors
A. Ceramic Capacitors
Ceramic capacitors are widely used due to their small size, low cost, and excellent stability. They are made from ceramic materials that serve as dielectrics, providing reliable performance in various applications.
B. Electrolytic Capacitors
Electrolytic capacitors are polarized capacitors that offer high capacitance values in a compact form. They are commonly used in power supply circuits and audio applications, where large capacitance is needed.
C. Film Capacitors
Film capacitors utilize thin plastic films as dielectrics. They are known for their stability, low loss, and high insulation resistance, making them suitable for high-frequency applications.
D. Tantalum Capacitors
Tantalum capacitors are known for their high capacitance-to-volume ratio and reliability. They are often used in applications where space is limited, such as in mobile devices and aerospace electronics.
E. Comparison of Different Types
Each type of capacitor has its advantages and disadvantages, making them suitable for specific applications. For instance, while ceramic capacitors are ideal for high-frequency applications, electrolytic capacitors are preferred for power supply circuits due to their high capacitance.
III. Raw Materials Used in Capacitor Production
A. Dielectric Materials
1. Types of Dielectrics
The dielectric material is a critical component of capacitors, influencing their performance. Common dielectric materials include ceramic, polyester, polypropylene, and tantalum oxide.
2. Properties Required for Dielectrics
Dielectrics must possess high insulation resistance, low dielectric loss, and stability over a range of temperatures and frequencies. These properties ensure that capacitors function effectively in various environments.
B. Conductive Materials
1. Metals Used (e.g., Aluminum, Tantalum)
Conductive materials, such as aluminum and tantalum, are used for the electrodes in capacitors. These metals are chosen for their excellent conductivity and compatibility with dielectric materials.
2. Conductive Coatings
In some capacitor designs, conductive coatings are applied to enhance conductivity and improve performance. These coatings can be made from various materials, including silver and copper.
C. Packaging Materials
1. Types of Packaging
Packaging materials protect capacitors from environmental factors and mechanical stress. Common packaging types include plastic, metal cans, and ceramic enclosures.
2. Importance of Packaging in Capacitor Performance
Proper packaging is essential for maintaining the integrity and performance of capacitors. It prevents moisture ingress, physical damage, and ensures reliable operation in various applications.
IV. The Production Process
A. Design and Engineering
1. Specifications and Requirements
The production process begins with design and engineering, where specifications for the capacitors are established. This includes determining capacitance values, voltage ratings, and physical dimensions.
2. Prototyping and Testing
Prototyping is a crucial step that allows manufacturers to test designs and make necessary adjustments before mass production. This phase often involves rigorous testing to ensure that the capacitors meet performance standards.
B. Material Preparation
1. Sourcing and Quality Control
Raw materials are sourced from suppliers, and quality control measures are implemented to ensure that they meet the required specifications. This step is vital for maintaining the overall quality of the final product.
2. Material Processing Techniques
Materials undergo various processing techniques, such as cutting, layering, and coating, to prepare them for assembly. These techniques are tailored to the specific type of capacitor being produced.
C. Manufacturing Steps
1. Layering and Assembly
a. Dielectric Layering
The dielectric material is layered according to the design specifications. This step is critical for determining the capacitor's performance characteristics.
b. Electrode Placement
Electrodes are then placed on the dielectric layers, ensuring proper alignment and contact. This step is essential for achieving the desired capacitance.
2. Encapsulation
a. Methods of Encapsulation
Encapsulation protects the internal components of the capacitor from environmental factors. Various methods, such as resin coating and heat-shrink tubing, are used depending on the capacitor type.
b. Importance of Encapsulation
Encapsulation is crucial for ensuring the longevity and reliability of capacitors, especially in harsh environments.
3. Electrical Testing
a. Testing Procedures
Once assembled, capacitors undergo electrical testing to verify their performance. This includes measuring capacitance, leakage current, and equivalent series resistance (ESR).
b. Quality Assurance
Quality assurance measures are implemented to ensure that only capacitors meeting the required specifications are released for distribution.
D. Final Assembly and Packaging
1. Final Inspection
Before packaging, capacitors undergo a final inspection to check for defects and ensure compliance with quality standards.
2. Packaging for Distribution
Capacitors are then packaged for distribution, ensuring that they are protected during transportation and storage.
V. Quality Control Measures
A. In-Process Quality Control
In-process quality control measures are implemented throughout the production process to identify and address issues early, ensuring consistent quality.
B. End-of-Line Testing
End-of-line testing is conducted on finished products to verify that they meet performance specifications before being shipped to customers.
C. Compliance with Industry Standards
1. ISO Standards
Manufacturers often adhere to ISO standards to ensure quality management and continuous improvement in their production processes.
2. RoHS Compliance
Compliance with RoHS (Restriction of Hazardous Substances) regulations is essential for ensuring that capacitors are free from harmful materials, promoting environmental sustainability.
VI. Challenges in Capacitor Production
A. Material Sourcing Issues
Sourcing high-quality materials can be challenging, especially with fluctuating market prices and availability of raw materials.
B. Technological Advancements
Keeping up with technological advancements in capacitor design and manufacturing processes is essential for maintaining competitiveness in the market.
C. Environmental Considerations
Manufacturers must address environmental concerns related to waste management and the use of hazardous materials in capacitor production.
D. Market Demand Fluctuations
Market demand for capacitors can fluctuate, impacting production schedules and inventory management.
VII. Future Trends in Capacitor Production
A. Innovations in Materials
Research into new dielectric and conductive materials is ongoing, with the aim of improving capacitor performance and reducing costs.
B. Advances in Manufacturing Techniques
Advancements in manufacturing techniques, such as automation and additive manufacturing, are expected to enhance production efficiency and reduce waste.
C. Sustainability Practices
Sustainability practices are becoming increasingly important, with manufacturers seeking to minimize their environmental impact through eco-friendly materials and processes.
D. Impact of Emerging Technologies (e.g., Electric Vehicles, Renewable Energy)
The rise of electric vehicles and renewable energy technologies is driving demand for high-performance capacitors, leading to innovations in design and production.
VIII. Conclusion
A. Summary of the Production Process
The production process of parallel capacitors involves a series of well-defined steps, from material selection to final assembly and testing. Each stage is critical for ensuring the quality and performance of the final product.
B. Importance of Continuous Improvement in Manufacturing
Continuous improvement in manufacturing processes is essential for meeting the evolving demands of the electronics industry and maintaining competitiveness.
C. Future Outlook for Parallel Capacitors in Electronics
As technology continues to advance, the demand for high-quality parallel capacitors will only increase. Manufacturers must adapt to these changes, embracing innovation and sustainability to thrive in the future.
IX. References
A. Academic Journals
B. Industry Reports
C. Manufacturer Guidelines
D. Standards Organizations
This blog post provides a comprehensive overview of the mainstream production process of parallel capacitors, highlighting the importance of each step and the challenges faced by manufacturers. By understanding this process, readers can appreciate the complexity and significance of capacitors in modern electronics.