What Components and Modules Do Ceramic Capacitors Contain?
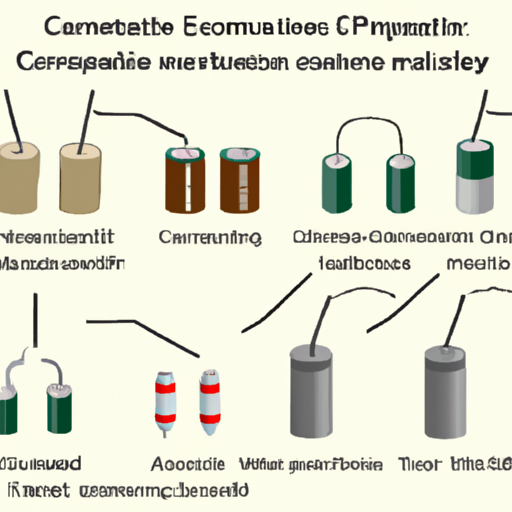
I. Introduction
A. Definition of Ceramic Capacitors
Ceramic capacitors are passive electronic components that store electrical energy in an electric field. They are made from ceramic materials that act as dielectric insulators, allowing them to hold charge when a voltage is applied. These capacitors are widely used in various electronic circuits due to their reliability, stability, and versatility.
B. Importance of Ceramic Capacitors in Electronics
Ceramic capacitors play a crucial role in modern electronics. They are essential for filtering, decoupling, and energy storage in a wide range of applications, from consumer electronics to industrial machinery. Their ability to operate at high frequencies and withstand high voltages makes them indispensable in many electronic designs.
C. Overview of the Article
This article will explore the components and modules that make up ceramic capacitors, including their basic structure, various types, manufacturing processes, and applications. Understanding these elements is vital for anyone involved in electronics design or manufacturing.
II. Basic Structure of Ceramic Capacitors
A. Dielectric Material
1. Description of Ceramic Dielectrics
The dielectric material in ceramic capacitors is typically a ceramic compound that exhibits high dielectric strength and low loss. This material is crucial for the capacitor's ability to store energy and maintain its performance under varying electrical conditions.
2. Types of Ceramic Dielectrics (Class 1 and Class 2)
Ceramic dielectrics are categorized into two main classes:
Class 1 Dielectrics: These materials offer stable capacitance over a wide range of temperatures and voltages. They are typically used in applications requiring precision, such as timing circuits and RF applications.
Class 2 Dielectrics: These materials provide higher capacitance values but with less stability. They are often used in applications where size and capacitance are more critical than precision, such as decoupling and filtering.
B. Electrodes
1. Function of Electrodes
Electrodes in ceramic capacitors serve as the conductive plates that store electrical charge. When a voltage is applied across the electrodes, an electric field is created in the dielectric material, allowing the capacitor to store energy.
2. Materials Used for Electrodes (e.g., Silver, Nickel)
Common materials for electrodes include silver and nickel. Silver is often used for its excellent conductivity, while nickel is more cost-effective and provides good performance in many applications. The choice of electrode material can influence the capacitor's performance, including its reliability and cost.
C. Capacitor Body
1. Construction and Form Factor
The capacitor body is the physical structure that houses the dielectric and electrodes. It can come in various form factors, including disc, rectangular, and multilayer configurations. The design of the capacitor body affects its size, capacitance, and application suitability.
2. Encapsulation and Protection
To protect the internal components from environmental factors such as moisture and mechanical stress, ceramic capacitors are often encapsulated in protective materials. This encapsulation can also enhance the capacitor's thermal stability and reliability.
III. Components of Ceramic Capacitors
A. Dielectric Layer
1. Role in Energy Storage
The dielectric layer is the heart of the ceramic capacitor, responsible for storing electrical energy. When a voltage is applied, the dielectric material polarizes, creating an electric field that holds the charge.
2. Influence on Capacitance and Voltage Ratings
The properties of the dielectric material, including its thickness and permittivity, directly influence the capacitor's capacitance and voltage ratings. Thicker dielectrics generally result in lower capacitance, while materials with higher permittivity can increase capacitance without increasing size.
B. Electrodes
1. Types of Electrodes (Internal vs. External)
Ceramic capacitors can have internal or external electrodes. Internal electrodes are embedded within the dielectric layers, allowing for a compact design, while external electrodes are attached to the capacitor's surface, making them easier to connect in circuits.
2. Connection Methods (e.g., Surface Mount, Through-Hole)
Connection methods for ceramic capacitors vary based on their design. Surface mount capacitors are soldered directly onto the surface of a circuit board, while through-hole capacitors have leads that pass through holes in the board. Each method has its advantages, depending on the application and design requirements.
C. Terminals
1. Types of Terminals (e.g., Leaded, Surface Mount)
Terminals are the points of connection for the capacitor in a circuit. Leaded terminals are used in traditional through-hole designs, while surface mount terminals are used in modern compact designs. The choice of terminal type affects the capacitor's integration into electronic circuits.
2. Importance in Circuit Integration
The design and type of terminals are critical for ensuring reliable connections in electronic circuits. Proper terminal design can enhance solderability, reduce parasitic inductance, and improve overall circuit performance.
IV. Modules and Variants of Ceramic Capacitors
A. Multilayer Ceramic Capacitors (MLCCs)
1. Structure and Functionality
Multilayer ceramic capacitors (MLCCs) consist of multiple layers of dielectric material and electrodes stacked together. This design allows for higher capacitance values in a smaller footprint, making MLCCs popular in compact electronic devices.
2. Applications and Advantages
MLCCs are widely used in consumer electronics, automotive applications, and telecommunications due to their high capacitance, low equivalent series resistance (ESR), and excellent frequency response. Their compact size and reliability make them ideal for modern electronic designs.
B. Single-Layer Ceramic Capacitors
1. Characteristics and Use Cases
Single-layer ceramic capacitors are simpler in design, consisting of a single dielectric layer and two electrodes. They are typically used in applications where lower capacitance values are sufficient, such as in bypass and coupling applications.
C. Specialty Ceramic Capacitors
1. High-Voltage Capacitors
High-voltage ceramic capacitors are designed to operate under extreme voltage conditions. They are used in applications such as power supplies and industrial equipment, where reliability and performance are critical.
2. Temperature-Stable Capacitors
Temperature-stable ceramic capacitors maintain their capacitance over a wide temperature range. These capacitors are essential in precision applications, such as oscillators and timing circuits, where temperature variations can affect performance.
V. Manufacturing Process of Ceramic Capacitors
A. Material Selection
1. Choosing Dielectric and Electrode Materials
The manufacturing process begins with selecting appropriate dielectric and electrode materials. The choice depends on the desired electrical characteristics, such as capacitance, voltage rating, and temperature stability.
B. Fabrication Techniques
1. Layering and Coating Processes
The fabrication of ceramic capacitors involves layering the dielectric material and applying electrodes. This can be done through various techniques, including screen printing and tape casting, to achieve the desired thickness and uniformity.
2. Sintering and Curing
After layering, the capacitors undergo sintering, a process that involves heating the materials to fuse them together. This step is crucial for achieving the desired electrical properties and mechanical strength.
C. Quality Control Measures
1. Testing for Capacitance, Voltage, and Reliability
Quality control is essential in the manufacturing of ceramic capacitors. Each capacitor is tested for capacitance, voltage rating, and reliability to ensure it meets industry standards and customer specifications.
VI. Applications of Ceramic Capacitors
A. Consumer Electronics
Ceramic capacitors are ubiquitous in consumer electronics, including smartphones, tablets, and laptops. They are used for decoupling, filtering, and energy storage, contributing to the overall performance and reliability of these devices.
B. Automotive Industry
In the automotive industry, ceramic capacitors are used in various applications, including engine control units, infotainment systems, and safety features. Their ability to withstand harsh conditions and high voltages makes them ideal for automotive applications.
C. Industrial Equipment
Ceramic capacitors are also used in industrial equipment, where they provide reliable performance in power supplies, motor drives, and control systems. Their robustness and stability under varying conditions are critical for industrial applications.
D. Telecommunications
In telecommunications, ceramic capacitors are essential for signal processing, filtering, and energy storage in devices such as routers, switches, and base stations. Their high-frequency performance and reliability are crucial for maintaining communication quality.
VII. Conclusion
A. Summary of Key Points
Ceramic capacitors are vital components in modern electronics, characterized by their unique structure, including dielectric materials, electrodes, and terminals. Understanding the components and modules of ceramic capacitors is essential for designing and manufacturing reliable electronic devices.
B. Future Trends in Ceramic Capacitor Technology
As technology advances, the demand for smaller, more efficient capacitors continues to grow. Future trends may include the development of new dielectric materials, improved manufacturing techniques, and enhanced performance characteristics to meet the needs of emerging applications.
C. Final Thoughts on the Importance of Understanding Components and Modules
A thorough understanding of the components and modules of ceramic capacitors is crucial for engineers and designers in the electronics industry. By grasping the intricacies of these components, professionals can make informed decisions that enhance the performance and reliability of their electronic designs. As technology evolves, staying informed about advancements in ceramic capacitor technology will be essential for continued innovation in the field.
What Components and Modules Do Ceramic Capacitors Contain?
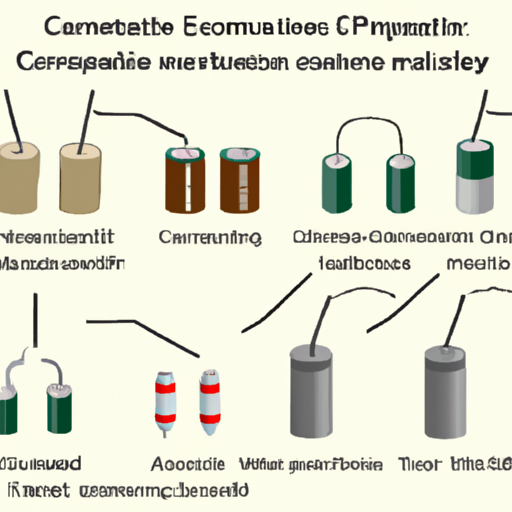
I. Introduction
A. Definition of Ceramic Capacitors
Ceramic capacitors are passive electronic components that store electrical energy in an electric field. They are made from ceramic materials that act as dielectric insulators, allowing them to hold charge when a voltage is applied. These capacitors are widely used in various electronic circuits due to their reliability, stability, and versatility.
B. Importance of Ceramic Capacitors in Electronics
Ceramic capacitors play a crucial role in modern electronics. They are essential for filtering, decoupling, and energy storage in a wide range of applications, from consumer electronics to industrial machinery. Their ability to operate at high frequencies and withstand high voltages makes them indispensable in many electronic designs.
C. Overview of the Article
This article will explore the components and modules that make up ceramic capacitors, including their basic structure, various types, manufacturing processes, and applications. Understanding these elements is vital for anyone involved in electronics design or manufacturing.
II. Basic Structure of Ceramic Capacitors
A. Dielectric Material
1. Description of Ceramic Dielectrics
The dielectric material in ceramic capacitors is typically a ceramic compound that exhibits high dielectric strength and low loss. This material is crucial for the capacitor's ability to store energy and maintain its performance under varying electrical conditions.
2. Types of Ceramic Dielectrics (Class 1 and Class 2)
Ceramic dielectrics are categorized into two main classes:
Class 1 Dielectrics: These materials offer stable capacitance over a wide range of temperatures and voltages. They are typically used in applications requiring precision, such as timing circuits and RF applications.
Class 2 Dielectrics: These materials provide higher capacitance values but with less stability. They are often used in applications where size and capacitance are more critical than precision, such as decoupling and filtering.
B. Electrodes
1. Function of Electrodes
Electrodes in ceramic capacitors serve as the conductive plates that store electrical charge. When a voltage is applied across the electrodes, an electric field is created in the dielectric material, allowing the capacitor to store energy.
2. Materials Used for Electrodes (e.g., Silver, Nickel)
Common materials for electrodes include silver and nickel. Silver is often used for its excellent conductivity, while nickel is more cost-effective and provides good performance in many applications. The choice of electrode material can influence the capacitor's performance, including its reliability and cost.
C. Capacitor Body
1. Construction and Form Factor
The capacitor body is the physical structure that houses the dielectric and electrodes. It can come in various form factors, including disc, rectangular, and multilayer configurations. The design of the capacitor body affects its size, capacitance, and application suitability.
2. Encapsulation and Protection
To protect the internal components from environmental factors such as moisture and mechanical stress, ceramic capacitors are often encapsulated in protective materials. This encapsulation can also enhance the capacitor's thermal stability and reliability.
III. Components of Ceramic Capacitors
A. Dielectric Layer
1. Role in Energy Storage
The dielectric layer is the heart of the ceramic capacitor, responsible for storing electrical energy. When a voltage is applied, the dielectric material polarizes, creating an electric field that holds the charge.
2. Influence on Capacitance and Voltage Ratings
The properties of the dielectric material, including its thickness and permittivity, directly influence the capacitor's capacitance and voltage ratings. Thicker dielectrics generally result in lower capacitance, while materials with higher permittivity can increase capacitance without increasing size.
B. Electrodes
1. Types of Electrodes (Internal vs. External)
Ceramic capacitors can have internal or external electrodes. Internal electrodes are embedded within the dielectric layers, allowing for a compact design, while external electrodes are attached to the capacitor's surface, making them easier to connect in circuits.
2. Connection Methods (e.g., Surface Mount, Through-Hole)
Connection methods for ceramic capacitors vary based on their design. Surface mount capacitors are soldered directly onto the surface of a circuit board, while through-hole capacitors have leads that pass through holes in the board. Each method has its advantages, depending on the application and design requirements.
C. Terminals
1. Types of Terminals (e.g., Leaded, Surface Mount)
Terminals are the points of connection for the capacitor in a circuit. Leaded terminals are used in traditional through-hole designs, while surface mount terminals are used in modern compact designs. The choice of terminal type affects the capacitor's integration into electronic circuits.
2. Importance in Circuit Integration
The design and type of terminals are critical for ensuring reliable connections in electronic circuits. Proper terminal design can enhance solderability, reduce parasitic inductance, and improve overall circuit performance.
IV. Modules and Variants of Ceramic Capacitors
A. Multilayer Ceramic Capacitors (MLCCs)
1. Structure and Functionality
Multilayer ceramic capacitors (MLCCs) consist of multiple layers of dielectric material and electrodes stacked together. This design allows for higher capacitance values in a smaller footprint, making MLCCs popular in compact electronic devices.
2. Applications and Advantages
MLCCs are widely used in consumer electronics, automotive applications, and telecommunications due to their high capacitance, low equivalent series resistance (ESR), and excellent frequency response. Their compact size and reliability make them ideal for modern electronic designs.
B. Single-Layer Ceramic Capacitors
1. Characteristics and Use Cases
Single-layer ceramic capacitors are simpler in design, consisting of a single dielectric layer and two electrodes. They are typically used in applications where lower capacitance values are sufficient, such as in bypass and coupling applications.
C. Specialty Ceramic Capacitors
1. High-Voltage Capacitors
High-voltage ceramic capacitors are designed to operate under extreme voltage conditions. They are used in applications such as power supplies and industrial equipment, where reliability and performance are critical.
2. Temperature-Stable Capacitors
Temperature-stable ceramic capacitors maintain their capacitance over a wide temperature range. These capacitors are essential in precision applications, such as oscillators and timing circuits, where temperature variations can affect performance.
V. Manufacturing Process of Ceramic Capacitors
A. Material Selection
1. Choosing Dielectric and Electrode Materials
The manufacturing process begins with selecting appropriate dielectric and electrode materials. The choice depends on the desired electrical characteristics, such as capacitance, voltage rating, and temperature stability.
B. Fabrication Techniques
1. Layering and Coating Processes
The fabrication of ceramic capacitors involves layering the dielectric material and applying electrodes. This can be done through various techniques, including screen printing and tape casting, to achieve the desired thickness and uniformity.
2. Sintering and Curing
After layering, the capacitors undergo sintering, a process that involves heating the materials to fuse them together. This step is crucial for achieving the desired electrical properties and mechanical strength.
C. Quality Control Measures
1. Testing for Capacitance, Voltage, and Reliability
Quality control is essential in the manufacturing of ceramic capacitors. Each capacitor is tested for capacitance, voltage rating, and reliability to ensure it meets industry standards and customer specifications.
VI. Applications of Ceramic Capacitors
A. Consumer Electronics
Ceramic capacitors are ubiquitous in consumer electronics, including smartphones, tablets, and laptops. They are used for decoupling, filtering, and energy storage, contributing to the overall performance and reliability of these devices.
B. Automotive Industry
In the automotive industry, ceramic capacitors are used in various applications, including engine control units, infotainment systems, and safety features. Their ability to withstand harsh conditions and high voltages makes them ideal for automotive applications.
C. Industrial Equipment
Ceramic capacitors are also used in industrial equipment, where they provide reliable performance in power supplies, motor drives, and control systems. Their robustness and stability under varying conditions are critical for industrial applications.
D. Telecommunications
In telecommunications, ceramic capacitors are essential for signal processing, filtering, and energy storage in devices such as routers, switches, and base stations. Their high-frequency performance and reliability are crucial for maintaining communication quality.
VII. Conclusion
A. Summary of Key Points
Ceramic capacitors are vital components in modern electronics, characterized by their unique structure, including dielectric materials, electrodes, and terminals. Understanding the components and modules of ceramic capacitors is essential for designing and manufacturing reliable electronic devices.
B. Future Trends in Ceramic Capacitor Technology
As technology advances, the demand for smaller, more efficient capacitors continues to grow. Future trends may include the development of new dielectric materials, improved manufacturing techniques, and enhanced performance characteristics to meet the needs of emerging applications.
C. Final Thoughts on the Importance of Understanding Components and Modules
A thorough understanding of the components and modules of ceramic capacitors is crucial for engineers and designers in the electronics industry. By grasping the intricacies of these components, professionals can make informed decisions that enhance the performance and reliability of their electronic designs. As technology evolves, staying informed about advancements in ceramic capacitor technology will be essential for continued innovation in the field.